Multiple-Stage Cementing
Multiple-stage cementing has typically been used in downhole formations that cannot support the hydrostatic pressure of a long column of cement. Today, specialized cement formulations make it more practical to carry out single stage cementing operations in many such formations. In some situations however, stage cementing remains an option. These can include:
- When cement is not required between widely separated intervals
- When the upper portion of an annulus must be cemented with a higher-density cement system
- In deep, hot holes where time to pump the desired quality and quantity of cement is limited and thus slurry pumpability is best maintained by reducing the total volume to be placed in an interval during any particular pumping operation
- In horizontal wells where the bend radius of the well requires cementing
There are essentially three multi-stage techniques:
- Regular two-stage cementing, where the cementing of each stage is a distinct operation
- Continuous two-stage cementing
- Three-stage cementing
The second and third techniques are rarely employed.
Multi-stage cementing adds to the execution time of a cement job and, because most cementing heads cannot accommodate the preloading of all of the devices needed to carry out a multi-stage operation, the cement head must be opened during the procedure, adding to the complexity.
A casing string set up for multi-stage cementing includes one or more stage cementing collars designed to be opened and closed by pressure-operated sliding sleeves. These collars provide a port for cement to be circulated to the annulus without going around the casing shoe.
First Stage Cementing Operations
The mixing and pumping of spacers and slurry during the first stage of a multi-stage cement job are essentially the same as a single stage job except there often is no bottom wiper plug. After pumping the slurry, the first stage wiper plug is dropped and lands in the float collar (Figure 1). In some situations, operators displace the first stage cement slurry with a completion fluid, leaving the casing below the stage collar filled with completion fluid.
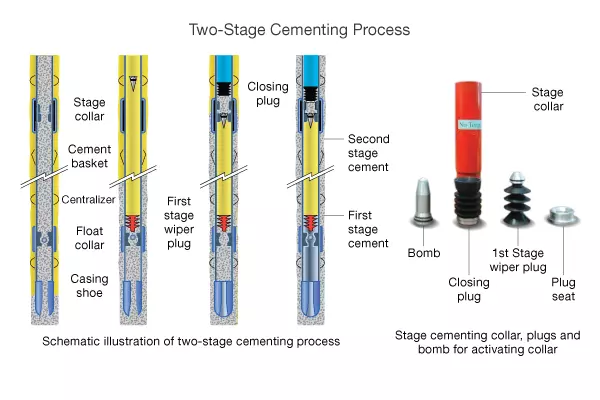
If the plan is to cement the entire casing string, the first stage cement slurry volume should be calculated to extend above the stage collar in the annulus. If not, the second stage cement slurry can fall through the less dense annulus fluid and result in a poor second-stage cement job. In some cases a cementing basket is run on the outside of the casing to prevent the cement slurry from falling.
Second Stage Cementing Operations
Immediately after the first stage is completed, a opening “bomb” is dropped to engage the internal structure of the stage collar.
When the bomb is seated, pump pressure (usually 1,200 to 1,500 psi) is applied, shearing the retaining pins and allowing a sliding sleeve to move and uncover ports to the annulus. In some cases (such as horizontal wells in which there is no gravity to make the bomb fall), hydraulically operated stage collars open when pump pressure is applied against the first stage plug.
When the ports open, they permit the first stage cement sitting above the stage collar to be circulated up the annulus and the well is circulated via the ports until the mud is properly conditioned and the first stage cement has set. This is important to ensure that weak zones along the first stage section do not break down when the hydrostatic column of the second stage cement is imposed.
In cementing the second stage, spacers and slurries are mixed and pumped in the same manner as a single stage job. The closing plug is dropped and pumped to seat in the stage collar. At this point, at least 1,500 psi (10.5 MPa) of pump pressure is applied to close the ports in the stage collar. Pressure is then released and the cement is allowed to reach its final set strength.
Most second stage cementing procedures are performed using a low-density slurry to allow circulation to the surface. Normal-density slurries are used when a high-pressure zone or aquifer must be thoroughly isolated. The density of the tail slurry of the second stage can be increased to enhance the cement strength around the stage collar, which is most likely to be the weakest point in the casing string.
Continuous Two-Stage Cementing Operations
If the situation requires that the cement be displaced without stopping to wait for a bomb to be seated, the two-stage operation can be accomplished in a continuous mode. In this case, which is rarely used, a wiper plug follows the first stage, and displacement fluid behind the plug places the first stage cement outside the annulus. A stage collar opening plug is pumped, followed immediately by the second stage cement slurry and the closing plug. Displacement of the slurry will cause the opening plug to seat, the collar to open, and the slurry to be displaced into the annulus. Final closure of the tool after seating of the closing plug is the same as with conventional two-stage cementing.
Three-Stage Cementing Operations
This option is rarely applied, because it significantly increases the time required and the complexity of the operation, increasing the potential for malfunctions to threaten the success of the cementing operation. In this case, both a second-stage collar and a third-stage collar are included in the casing string, and two sequences of sealing plugs, bombs and closing plugs must be dropped for the job to be completed.