Environmental Aspects of Fracturing Fluids
As hydraulic fracturing has taken on an increasingly significant role in oil and gas development, concerns have arisen over its environmental impact. In the United States, Europe and elsewhere, these concerns have brought about efforts to restrict shale gas development and other activities that rely on large-volume hydraulic fracturing to be successful.
The key issues related specifically to hydraulic fracturing fluids appear to be:
- Long-term impact of withdrawing large volumes of fresh water from the water cycle.
- Risks of damage to surface sources of fresh water during the transportation, handling and treatment of fracturing flowback water and produced water.
- Risks of contaminating relatively shallow subsurface sources of fresh water during the drilling and hydraulic fracturing processes.
Sources of Fresh Water
Choosing a source for fresh water as makeup water for hydraulic fracturing fluid is driven by cost and availability. In places like the Appalachian basin of the United States (home to the Marcellus Shale and Utica-Point Pleasant Shale plays), the cheapest and most easily available sources of freshwater are surface sources such as rivers, lakes, ponds, and streams. In the state of West Virginia, between 2009 and mid-2014, the sources of fracturing makeup water were 83.5 percent surface sources, 12.4 percent recycled water from previous fracturing treatments, and 3 percent subsurface groundwater (West Virginia, 2013).
In more arid places like parts of Texas, where a similar high level of hydraulic fracturing is under way, there are fewer surface water sources and the distribution may be skewed more towards subsurface sources (Nicot et al, 2011).
The volumes of water used for fracturing shale wells in the various shale plays currently under development in the U.S. are large, ranging from 1 to >6 million gallons per well. While recycling of the fracturing fluid that flows back after a treatment is increasing, it still makes up a relatively small portion of the total makeup water in most plays—less than 20 percent. Part of the reason for this is that in many of the shale plays under development in the United States, the volume of fracturing fluid that flows back soon after the well is put on production is on the order of about 10 to 35 percent of what is injected. This share may increase over time but a majority of the water that is injected appears to remain in the formation.
Another reason is that the cost of recycling must be compared to the cost of disposing of the flowback water and acquiring new fresh water for subsequent fracturing treatments. Where disposal costs and fresh water acquisition costs are relatively low, recycling may not make economic sense.
All of these alternatives must be considered within the context of the specific situation or play. The behavior of the formation, the relative costs of various options, and other factors (such as regulations) must be taken into account. These all vary among the different shale plays under development in the United States, and will certainly vary across the globe if and when large volume hydraulic fracturing becomes more common in other oil and natural gas producing regions.
While the volume of water used for hydraulic fracturing in the U.S. is large, it is still relatively small when compared to other uses: crop irrigation, cooling water for electric power generation, domestic water uses, and other industrial uses. Even in relatively arid Texas, as of 2011, the total annual water consumption for hydraulic fracturing in the Barnett Shale, the largest play in Texas, is about 9 percent of the annual water consumption of the city of Dallas, and total water use for all shale gas wells in Texas amounted to less than 1 percent of all freshwater withdrawals in the state. However, on a local basis, and in drought-stricken areas, demand for fresh water for fracturing can compete unfavorably with other uses.
Fracture Flowback Treatment and Disposal
The trends in water acquisition, transportation, handling, treatment, and disposal for large volume fracturing treatments in the U.S. vary somewhat depending on the region.
In the Fayetteville (Arkansas) and Marcellus (Pennsylvania) shale plays in particular, water is sourced largely from surface streams or rivers (Figure 1), and transported via temporary water line or tank trucks to impoundments (Figure 2) which can serve as a central source for multiple wells or multiple multi-well pads.
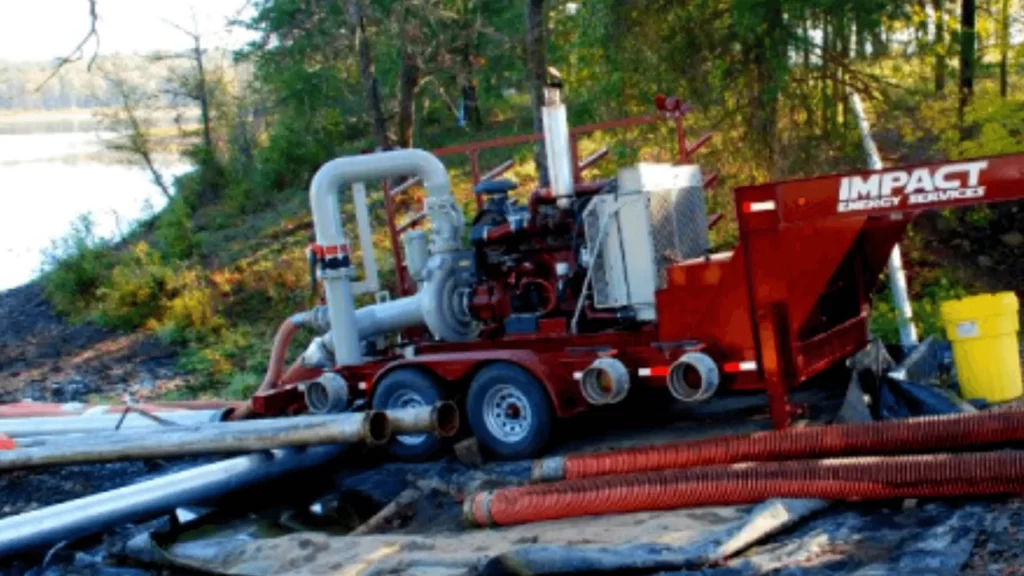

The water that flows back after fracturing generally contains a mixture of salts and other contaminants. This water is usually captured in tanks (Figure 3) and either treated for recycling or trucked to water disposal wells for deep injection. Operations that are performed on multiple well pads, where wells may be in various stages of completion and production, require careful planning with respect to water management. Such planning is one of the critical factors in optimizing the economics of shale play development in the U.S. (Figure 4).

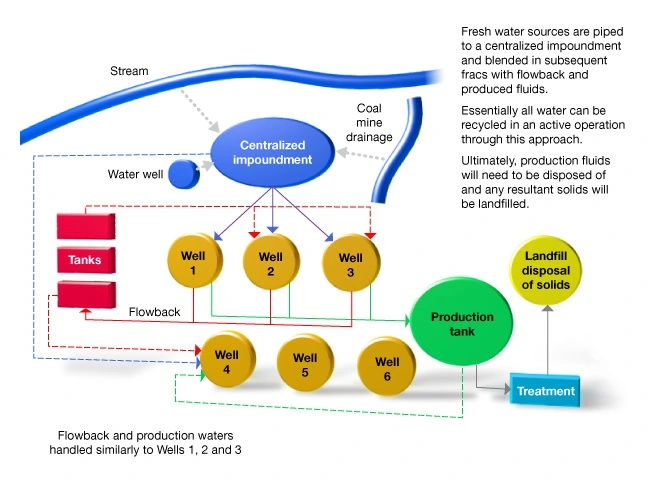
Figure 4: Water handling and recycling schematic for Marcellus Shale development
There are a number of options for treating the flowback water. Some are energy intensive (and thus more costly) but remove a large portion of the dissolved salts from the flowback water, resulting in a relatively fresh volume of water and a much smaller volume of concentrated brine that must be disposed of via injection. A more common approach has been to filter the flowback, removing debris, particulates and some portion of the dissolved salts, and add chemicals that make it possible to reuse this still-salty water in combination with a larger portion of fresh water. Companies operating in the Marcellus Shale play have been able to recycle nearly all of their flowback water in this manner, reducing their demand for freshwater by up to 20 percent.
Ensuring Environmental Safety
The environmental impact of hydraulic fracturing fluids has been a subject of concern and scrutiny. To address these concerns, extensive measures are taken to ensure the safe handling and disposal of these fluids. Proper containment systems, rigorous monitoring, and adherence to regulatory guidelines are crucial in mitigating potential risks and protecting both the environment and human health.
Mitigating Environmental Impacts
Efforts are continuously made to minimize the environmental impacts associated with hydraulic fracturing fluids. Innovations such as using biodegradable additives, reducing water consumption through recycling and treatment, and developing alternative fracturing fluids with lower toxicity are being explored. Additionally, best practices and stringent regulations are being implemented to prevent any leakage or contamination of groundwater.
Advances in Fracturing Fluid Technology
Advancements in fracturing fluid technology are revolutionizing the industry and improving the efficiency and sustainability of the fracking process. Researchers are exploring novel additives, nanotechnology, and advanced monitoring techniques to enhance fluid performance, reduce environmental impacts, and optimize resource recovery. These advancements have the potential to make hydraulic fracturing even more efficient and environmentally friendly in the future.
Future Prospects and Innovations
The future of hydraulic fracturing fluids holds exciting possibilities. Ongoing research and development aim to address the challenges associated with water usage, chemical additives, and environmental concerns. Alternative fracturing techniques, such as using foam or gel-based fluids, are being investigated to minimize the volume of water and additives required. Furthermore, advancements in data analytics and modeling are improving the understanding of fluid behavior and aiding in the design of more effective fracturing treatments.
Conclusion
Hydraulic fracturing fluids have revolutionized the energy industry by unlocking the vast potential of shale gas reserves. Through the careful selection and application of fluid compositions, the hydraulic fracturing process allows for the extraction of natural gas and oil from previously inaccessible rock formations.
While concerns regarding water usage, air emissions, and induced seismicity exist, the industry has made significant strides in addressing these issues. Stringent regulations, technological advancements, and best practices are continuously improving the safety and sustainability of hydraulic fracturing operations.
As the energy landscape evolves, ongoing research and innovation in hydraulic fracturing fluids will pave the way for more efficient, environmentally friendly, and responsible practices. By balancing the demand for energy with sound environmental stewardship, we can continue to harness the power of hydraulic fracturing fluids while minimizing their impact on our planet.