Learning Objectives
After completing this topic “Hydraulic Fracturing Fluids“, you will be able to:
- List the functions performed by fracturing fluids and their related properties.
- Relate the rheological properties of fracturing fluids to their performance characteristics.
- Describe the methods used to control fracturing fluids loss during fracking operations.
- Describe the common types of fracturing fluids systems and their areas of application.
- Discuss the types and functions of common fracturing fluids additives.
- Summarize the environmental issues involved in the use of fracturing fluids systems.
Introduction
Hydraulic fracturing fluids play a crucial role in the extraction of shale gas, revolutionizing the energy industry in recent years. As we delve into the world of hydraulic fracturing fluids, we will explore their composition, application, and environmental impact. This comprehensive guide will provide you with an in-depth understanding of the technology behind hydraulic fracturing fluids and shed light on the concerns surrounding their usage.
Hydraulic Fracturing Fluids: An Overview
Hydraulic fracturing fluids, commonly referred to as fracking fluids, are a combination of water, proppants, and chemical additives. These fluids are injected into underground shale formations at high pressure to create fractures and release natural gas or oil trapped within the rock. The process involves drilling deep into the earth’s crust and injecting the fluids to fracture the rock, allowing the extraction of valuable resources.
The Role of Hydraulic Fracturing Fluids
Hydraulic fracturing fluids serve multiple purposes during the fracking operation. Firstly, they act as a carrier for proppants, such as sand or ceramic beads, which prop open the fractures created in the rock formation. Secondly, these fluids contain various additives that optimize the fracturing process, improve fluid flow, prevent corrosion, and reduce the risk of microbial growth.
Fluid Functions and Properties
The functions of a fracturing fluid are to:
- Deliver the hydraulic energy needed to initiate a fracture.
- Propagate or extend the fracture.
- Transport and place proppant into the fracture.
- Return to the wellbore following the treatment.
In selecting a fluid to meet these requirements, job planners must consider health, safety and environmental (HSE) concerns, fluid cost and availability, logistical considerations, pumping capabilities and the interactions between the fluid and the formation.
Fracturing treatments most commonly use water as the base fluid. Other fluids in use include carbon dioxide, nitrogen, or liquefied petroleum gas (LPG) mixed with additives to create “energized” proppant-carrying foam, gelled fluids and acid solutions. Fluids may also be used in combination. Figure 1 illustrates the relative usage of various fluids for treatments in the United States over a one-year period.
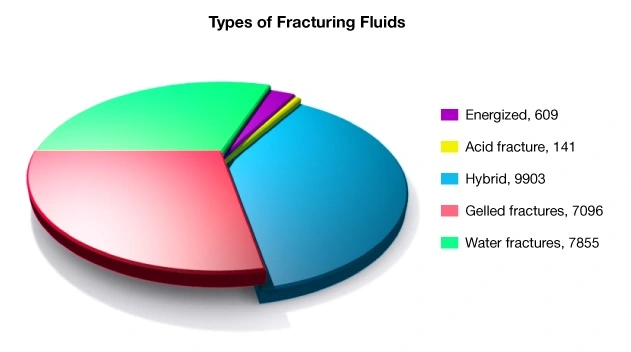
The basic functions of a fracturing fluid to initiate and propagate the fracture, transport and deliver proppant, and return to the wellbore after the treatment call for unique and sometimes contradictory fluid characteristics. A typical hydraulic fracturing treatment might call for several fluid stages, with each stage having different characteristics (Table 1):
Stage | Description | Function |
---|---|---|
1. Pre-pad | Water mixed with a dilute hydrochloric or muriatic acid | Clear debris from the wellbore and provide an open conduit for subsequent stages |
2. Pad | Mixture of water, polymer thickeners and other additives | Initiate and propagate the fracture |
3. Slurry | Mixture of pad plus a solid proppant such as sand; proppant concentration may vary throughout different stages of the treatement | Hold the proppant in suspension as it is delivered into the fracture; extend the fracture and transport the proppant out into the formation between the fracture faces |
4. Displacement | Fluid with no added proppant | Displace the proppant-laden slurry out of the wellbore |
If properly designed, the rate at which the pad fluid leaks off into the formation should be such that all of the fluid has gone into the formation once the fracture reaches its design length and the proppant is in place. If the pad leaks off too quickly, the fracture will be too short. If it leaks off too slowly, the proppant will not be carried to the outer extent of the fracture.
Table 2 shows an example of a fracturing treatment comprised of four slurry stages. For large, multi-stage fracturing treatments, such as those performed in long horizontal wells, a similar sequence of stages may be designed for each independent fluid stage.
Stage | Pump Rate (bbl/min) | Volume (gal) | Proppant Concentration (lbm/gal) | Estimated Surface Pressure (psi) |
---|---|---|---|---|
Pad | 35 | 5,000 | 0 | 5,630 |
Slurry | 35 | 9,000 | 2 | 4,610 |
Slurry | 35 | 14,000 | 4 | 3,760 |
Slurry | 35 | 23,000 | 6 | 3,080 |
Slurry | 35 | 15,000 | 8 | 2,460 |
Displacement | 35 | 13,200 | 0 | 6,170 |
Total | 79,200 |
Note in this example that the later stages typically have higher proppant concentrations. This common practice allows the slurry to leak off if it has farther to travel along the fracture. Larger-sized proppant particles may be used in the end slurry stage (the stage that remains closest to the wellbore) in order to reduce the chances of turbulent flow near the wellbore when the well is producing.
At a certain point in the displacement stage indicated by a rise in bottomhole pressure the proppant packs into the fracture tip. At this point, pumping is stopped, and the pressure within the fracture begins to decline as fluid leaks off. In response to this pressure reduction, the fracture begins to close. It is the proppant that prevents the fracture from closing completely and maintains a high-permeability flow channel within the fracture.
Relation between Fluid Functions and Properties
Table 3 summarizes the important functions of fracturing fluids at each stage of a treatment, and lists the properties that are favorable to carrying out these functions.
Function | Desirable Properties |
---|---|
Fracture Initiation | High leakoff rate; “penetrating fluid” with no fluid-loss control |
Fracture Propagation | Controlled leakoff rate Fluid viscosity sufficient to create desired fracture width |
Proppant Transport | Fluid viscosity high enough to maintain proppant-carrying ability |
Cleanup | Low-viscosity, for easy removal from the formation and production to surface Non-damaging; does not leave residue in the formation, and does not alter the chemical or physical nature of the formation in a manner that impedes flow |
Damage Resulting from Fracturing Treatments
Types of damage that can result from fracturing include:
- Proppant pack damage resulting from polymer residue in the proppant pack
- Fracture face damage, caused by a residual filter cake at the fracture face
- Formation damage caused by polymer residue that has leaked off into the formation
- Formation damage caused by non-compatibility of the fracturing fluid rock matrix (such as clay swelling)
The relative importance of these types of damage varies, depending on the formation permeability:
- For low and medium permeability fracturing, the major consideration should be to avoid proppant pack damage.
- In high permeability formations, the fracture face and formation damage increase in importance and may become critical.