Gas Supply and Compression Equipment
Gas supply and compression equipment is similar to that used for air and nitrogen drilling. The system should be designed to overcome the highest anticipated injection pressure. Gas injection rates should be monitored very closely in gasified liquid drilling to achieve the desired bottomhole pressure.
Parasite Tubing String
A parasite string can be either a regular jointed tubing or coiled tubing. It should be designed to withstand the same burst rating as its host casing.
One inch diameter tubing is typical for parasite string applications. However, for high gas injection rates, larger tubing may be required. The end of a parasite string is joined to casing using a sub shown in Figure 1.
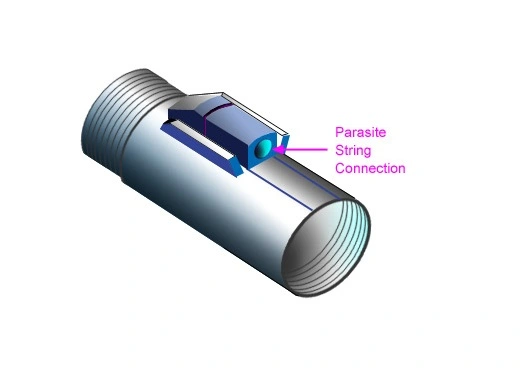
After the cement is placed, water is circulated down the parasite string to ensure that it is not plugged. The sub connection should be strong enough to withstand the pressures during cementing and other subsequent completion operations. Clamps are used to keep the parasite string straight outside the casing.
In the case of coiled tubing, the string is run over the gooseneck and through the rotary table with the casing. During the wellhead and BOP installation, the casing won’t be perfectly eccentric with the center of the rotary table. This can cause rapid wear on the rotating head and other sealing elements. The surface casing-parasite tubing assembly can be centered down the rotary table by adjusting the conductor pipe before the cement sets.
Annular Gas Injection
Gas can also be injected through a temporary secondary casing string inside the intermediate one. This might require larger diameter hole drilling since the intermediate casing size has to be increased to accommodate the secondary string (Figure 2).
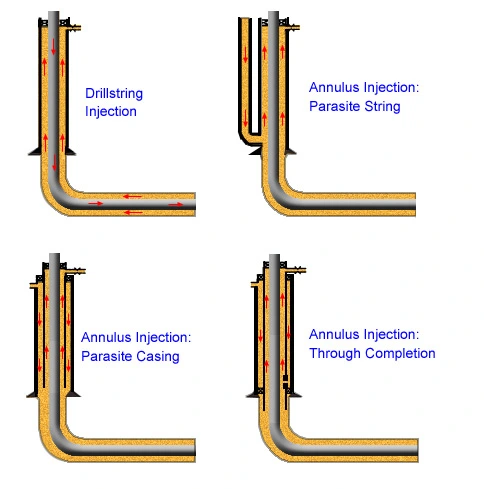
Special casing heads are used to hang off the additional casing string inside the intermediate string. It might also be possible to hang the temporary string inside conventional wellhead equipment. A check valve connects the gas supply to the wellhead. In the case of a shut-in well, this allows the supply gas to be isolated from the casing annulus.
Adequate supplies of kill fluids must be kept on site. As a rule of thumb, this quantity should be 1.5 times the well volume. Additional tanks may be required to hold this supply beyond the conventional mud tanks.