Gasified Liquid Drilling Overview
Whenever a gas is introduced into a flowing liquid, the liquid’s density will be reduced regardless of the structure of the final mixture. Gasified liquids, which are used for underbalanced drilling applications, generally do not contain surfactants. Bottomhole pressures are typically higher for gasified liquids since the liquid phase is the predominant phase. Effective densities range from 4 to 7 ppg.
In the past, most of the gasified drilling fluids were aerated muds. Their primary application was to avoid lost circulation. Reducing the density of drilling fluid by gasifying is a cost-effective way to avoid lost circulation.
Recent applications are predominantly for underbalanced drilling. Nitrogen or natural gas is used to gasify the base liquid, which is normally an unviscosified water or crude oil. Most of the applications are in horizontal wells where the production interval has a longer exposure to the drilling fluids. Stimulation of horizontal wells is more difficult and expensive. Therefore, drilling underbalanced is a better practice to avoid formation damage.
Gasified liquids provide a better hydraulic damping of the drillstring vibrations compared to dry gas or mist drilling. Moreover, drillstring components tend to show less erosive wear with gasified liquids.
Gasification Techniques
There are two basic techniques for introducing the gas into the drilling fluid:
1. Injecting gas into the liquid at the surface just before it enters the drillpipe.
- Advantages:
- No need for additional equipment
- Possible to achieve lower bottomhole pressures
- Gas injection rate for a particular bottomhole pressure is less compared to parasite tubing case
- Better bit hydraulics
- Disadvantages:
- Gasification can not be performed when circulation is shut down
- Two-phase flow down the drillpipe leads to higher frictional pressure losses
- Separate flow of gas and liquid through a downhole motor reduces its efficiency
- When drilling a permeable formation, the injected gas phase can infiltrate into the permeable formation
- Higher corrosion rates due to extended exposure of the drillstring to injected gas
2. Injecting gas downhole to the annulus. This technique requires the use of a parasite tubing string, which is run outside of the last string of casing as illustrated in Figure 1.
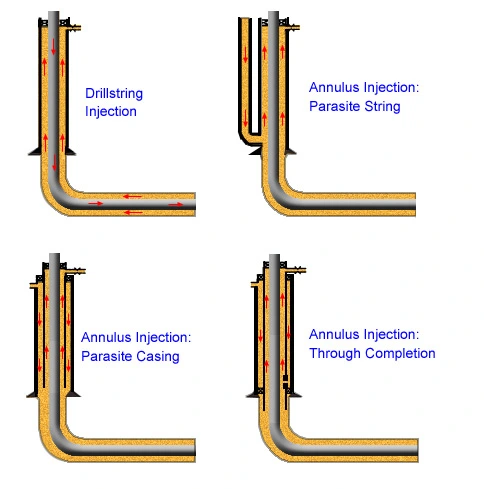
- Advantages:
- Continuous gasification of the drilling fluid even when making connections or tripping
- Single-phase flow in the drill string; MWD systems can be used
- Since the gas is introduced inside casing, the potential of flowing into exposed permeable formations is almost eliminated.
- Not all the drill string is exposed to the injected gas, resulting in less corrosion.
The Liquid Phase
Unweighted drilling muds are used as the liquid phase in gasified drilling fluids. Water, brine, diesel, crude oil or condensates are various options. Since inflows are highly likely during underbalanced drilling, it is better not to use conventional drilling mud as the liquid phase, because it may become very expensive to re-condition the diluted mud over time.
The base liquid should be compatible with formation fluids that may be encountered. Since transient overbalanced conditions may be experienced, the drilling fluid should also be non-damaging to any producing formation.
Emulsions are formed when formation water flows into a hydrocarbon-based, gasified liquid or when oil flows into a water-based, gasified liquid. In this case, it becomes difficult to control the downhole pressure. The presence of viscosifying and fluid loss control polymers can promote formation of emulsions. Addition of de-emulsifiers to the injected liquid is an effective solution to this problem.
Foaming at the surface may also present a problem. However, the minimal use of viscosifying agents can restrict this problem.
If water does not provide sufficient hole cleaning capacity, conventional drilling mud may be used as the liquid phase. The mud viscosity and gel strength have to be kept at a minimum to maintain low gas injection rates. Moreover, an atmospheric de-gasser is needed for removing the gas from low viscosity muds.
The Gas Phase
Air, nitrogen and natural gas are commonly used to gasify drilling fluids. The necessary injection pressure and rates are obtained by using compressors and a booster.
Aerated liquids are very corrosive. Good pH control corrosion inhibitors must be used to reduce the corrosion to manageable levels.
As long as the liquid phase is continuous, the risk of downhole fires with gasified liquid drilling is very low. However, in horizontal wells, as in foam drilling, the separation of air to the top and liquid to the bottom increase the likelihood of downhole fires. The use of nitrogen as the gas phase can completely eliminate the risk of downhole fires.
If the well requires high injection rates, both nitrogen and compressed air can be injected simultaneously. The composition of the mixture has to be checked carefully in order to avoid combustible proportions.
As is true for Nitrogen Drilling, the natural gas will not be combustible if the oxygen concentration is less than 8 percent.
As long as the risk of combustion is controlled, the selection of gas for a gasified drilling depends on the cost of the operation. The role of gas in this type of drilling is mainly to reduce the drilling fluid density, but not to clean the hole.
Rheology
Turbulent flow should be expected with gasified liquids. An annular velocity of 7 ft/min is high enough for turbulence. Typical annular velocities of gasified liquids are in excess of 100 ft/min. Basically the high annular velocities are more effective in hole cleaning than the fluid rheology.