Principal Components
The drill string is the conduit that transmits mechanical and hydraulic energy from the surface to the drill bit, with mechanical energy coming from the weight and rotation of the drill string, and hydraulic energy coming from the mud pumps and circulating drilling fluid. From top to bottom, it consists of a kelly or top-drive unit, drill pipe and a bottomhole assembly (Figure 1: Drill string schematic showing a “slick” (drill collars only) bottomhole assembly).

Kelly or Top Drive Unit
A kelly is a square or hexagonal length of pipe that fits into a bushing in the rig’s rotary table (Figure 2). As the rotary table turns to the right, the kelly turns with it. The kelly’s main function is to transfer energy from the rotary table to the drill string.

An alternative to the kelly/rotary table arrangement is the top-drive unit, which consists of a hydraulic or electric motor that turns the drill string using either a power swivel or a power sub located directly below a conventional swivel. (Figure 3). In a top-drive with an integral power swivel, drilling fluid enters the drill string through the top-drive unit.

A top-drive unit has several advantages over a kelly-rotary table assembly:
- Unlike a kelly, which requires making a new connection with each single joint of drill pipe, a top-drive unit makes it possible to drill with made-up, 90-ft triple stands. This reduces pipe connections, decreases drilling time and improves rig safety.
- A top-drive unit provides greater control of directional drilling tools and quicker tool orientation.
- With a top-drive unit, it is possible to ream with triple stands rather than single pipe joints.
- When tripping a drill string with a kelly assembly, it is necessary to shut down the mud pumps. But with a top-drive unit, it is possible to circulate mud and rotate while tripping the drill string, thus reducing the chances of stuck pipe.
- A top-drive provides for more accurate tool joint make-up, which can extend the life of drill pipe.
Drill Pipe
The longest portion of the drill string consists of connected lengths of drill pipe (Figure 4), which provides length to the drill string and transmits rotational and hydraulic energy to the bottomhole assembly and the drill bit.
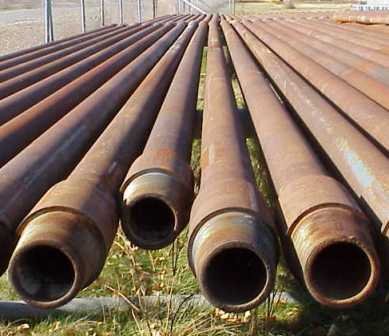
In a conventional (non-horizontal) well, the bottomhole assembly (BHA) is the portion of the drill string between the drill pipe and the drill bit. It may be configured in any number of ways to promote drilling objectives. The most commonly used BHA components are:
- Drill collars (Figure 5): These heavy, thick-walled tubulars impart stiffness to the drill string, maintain tension on the drill pipe, provide weight and stability to the drill bit, and help keep the hole on a straight course.

- Heavy wall drill pipe is lighter and thinner than drill collars, but heavier and thicker than drill pipe. Using it as an intermediate-weight drill string member between the drill pipe and drill collars can help reduce fatigue failures, providing additional hole stability and aiding in directional control.
- Stabilizers, strategically placed at various points in the BHA, help to centralize the drill collars, thereby reducing the risk of stuck pipe. They can also be used to maintain a full-gauge hole diameter and as an aid in controlling well trajectory.
- Crossover subs are used to join components having different types of connections.
Other tools may be used in the BHA based on well objectives or anticipated drilling conditions. For example:
- Mechanical or hydraulic drilling jars convert stored energy from the drill string to a sharp upward or downward impact force that can help free a stuck BHA.
- Rotary reamers can be used in hard or abrasive formations to maintain a full-gauge hole.
- Vibration dampeners can help absorb vibrations or shock loads that might otherwise contribute to drill string failure.
- Hole openers are used to increase the diameter of a drilled hole section.
- A float sub prevents drilling fluid from backflowing into the drill string and reduces the potential for swabbing.
- A circulating sub enables lost circulation material to be pumped without plugging the bit nozzles.
- Measurement While Drilling (MWD) tools include devices for measuring wellbore inclination and azimuth, downhole pressure, and drilling dynamics measurements such as shock and vibration.
- Logging While Drilling (LWD) tools provide real-time formation evaluation data similar to that obtained from wireline logging devices.
- Mud motors, commonly used in directional drilling, are positive-displacement downhole motors that employ a rotor-stator assembly to convert the hydraulic energy of the drilling fluid to mechanical energy that turns the drill bit. When a mud motor is used, the drill string does not rotate.
A well-designed bottomhole assembly helps maximize drilling rates, produce a smooth, full-size borehole, prevent drill pipe buckling, maintain directional control, avoid drilling problems, and prevent future completion and production problems.