Special Features
Drill collars may be fabricated with special features to improve their strength, ease of handling, downhole performance and recoverability in case fishing becomes necessary.
Non-Magnetic Drill Collars
Drill collars and other bottomhole assembly tools are usually made of plain carbon steel, which can cause magnetic interference with the compasses contained in directional survey tools. To reduce this interference, drill collars made of nickel-copper or other non-magnetic alloys can be run in the BHA sections where the compasses are to be located.
Square Drill Collars
In severe “crooked hole” drilling environments (e.g., steeply dipping bedding planes, fractured or faulted formations, extremely hard formations or hard-and-soft formation sequences), controlling wellbore deviation can be a particular challenge. In such cases, square drill collars can be run above the bit to centralize the bottomhole assembly, maximize its stiffness and torsional damping, and minimize axial vibrations. Their major disadvantages are that they are expensive to buy and maintain, they tend to create high rotary torque, they are difficult to fish, and they grind drilled cuttings to fines, thereby increasing mud consumption (Mitchell, 1995).
Spiral Grooves
Small-to-medium OD drill collars with spiral grooves (Figure 1) help prevent differential sticking by reducing the contact area between the collars and the borehole wall, and by allowing the hydrostatic mud pressure to equalize around the drill collars. Note that the weight of a round drill collar will be reduced by approximately 4% by spiral conversion.

Stepped Bores
Stepped bores (Figure 2) are reduced ID sections through pin connections of drill collars. They are used to increase the pin strength in small and medium diameter collars when large bores are needed for circulating fluid. A typical example would be a 6 1/4 inch drill collar with a 2 13/16 inch bore that is reduced to 2 1/4 inches through the pin.
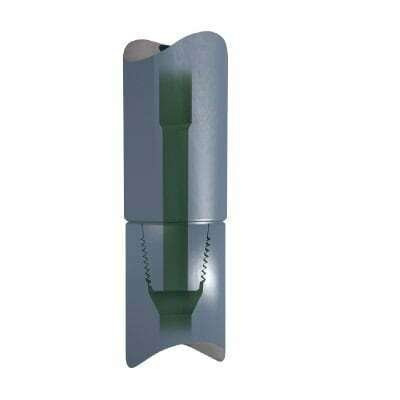
Slip and Elevator Recesses
Slip and elevator recesses (Figure 3) eliminate the need for safety clamps and lift subs, enabling the rig crew to simply change elevators and handle drill collars as they would handle drill pipe. Machining and repairing these recesses, however, requires extreme caution and close adherence to manufacturer specifications — even slight deviations in recess depth, curvature on the ends, surface finish and cold rolling can cause serious high stress problems. Slip and elevator recesses should not be used in highly corrosive environments because of the increased potential for stress corrosion.
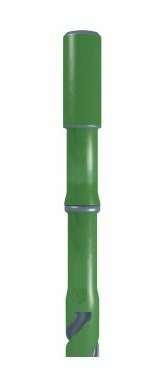
Fishing Neck
A fishing neck (Figure 4) — so called because of its ability to receive a fishing overshot and grapple in case the collar parts in the hole — is a section of reduced outside diameter at the end of a drill collar. It is machined to allow smaller connections, which can be properly torqued using available rig tongs and catheads. Fishing necks are common in drill collars of more than 8 inches outside diameter, but are occasionally found on smaller sizes when the clearance between the collar and the hole is very small.
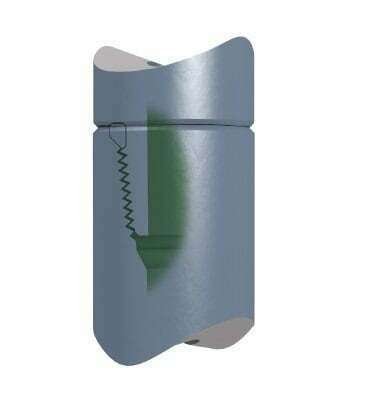
Hard-Facin
Many drill collars are hard-faced with tungsten carbide for areas where abrasive formations cause rapid outside diameter wear. As is the case with machining slip and elevator recesses, hard facing requires extreme care. The steel used in drill collars is very sensitive to quench effect, and can easily be cracked or left with high residual stresses that can cause cracks to form later. An additional concern is that rough hard-facing can result in costly casing wear.