Basic Cement Slurry Formation
Cement slurries, consisting of cement suspended in water (Figure 1), are usually prepared in the field by mixing the dry cement and dry additives with water and liquid additives. This can be done using a jet mixer, a batch mixer, or a recirculating mixer.
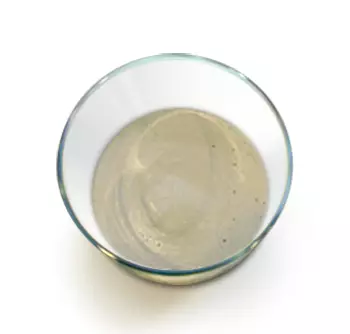
Figure 2 illustrates the components and operation of a continuous jet mixer. The benefits of this type of system are its simplicity and dependability, and the fact that it is not volume-limited. The rates of liquid injection and dry cement flow are carefully controlled to achieve slurry with a specific ratio of water to cement. The most important aspect of cement blending is obtaining a consistent slurry with the proper amount of additives and mix water.
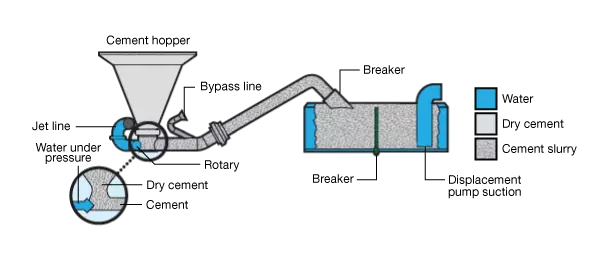
The principal disadvantage of a jet mixer is its inability to closely control slurry density. Various types of batch mixers utilizing either mechanical agitation or circulation are available for mixing up to 100 bbl (16 ) of cement slurry. This type of mixer can control density within a range of 0.2
.
For some operations it is useful to prepare the slurry with a jet mixer that discharges into a batch mixer, where final density adjustments may be made before the slurry is pumped into the well. Recirculating-type jet mixers, where a portion of the slurry is re-circulated through the mixer, can also be used to prepare slurries with a more uniform density. However, a perfectly acceptable slurry can be achieved by an experienced operator using a jet mixer, and jet mixers are used for almost all large jobs that require a constant supply of cement slurry at a high rate.
Cement Slurry Specifications
If the mixture contains no additives, it is termed “neat” cement. Table 1 shows the preferred water/cement ratio for the various API cement classes, as well as the resulting slurry densities. For example, a Class A “neat” slurry of cement and water should contain 46% mix water “by weight of cement” (BWOC). (For reference, the density of fresh water is 8.33 lbm per gallon and seawater is typically 8.54 lbm per gallon.)
Cement Class | Mix Water | Water/Cement Ratio | Slurry Density | Yield |
---|---|---|---|---|
(%BWOC) | ![]() | (ppg) | ![]() | |
A | 46 | 5.2 | 15.6 | 1.18 |
B | 46 | 5.2 | 15.6 | 1.18 |
C | 56 | 6.3 | 14.8 | 1.32 |
D, E, F | 38 | 4.3 | 16.45 | 1.05 |
G | 44 | 5.0 | 15.8 | 1.15 |
H | 38 | 4.3 | 16.45 | 1.05 |
The range of densities of these slurries results from the different degrees of fineness of the various types of API cement, which affect water requirement. Of the commonly used API types, Class C is the most finely ground, Classes A and G are intermediate, and Class H is the most coarsely ground. Slurries prepared with the finer grinds tend to show slightly lower cement-slurry-filtration rates.
The optimal water-to-cement ratio for a cement slurry is a compromise between pumpability and strength. For example, for Class G neat cement, the maximum cement strength occurs at a water-to-cement ratio of about 2.8 . This is the minimum amount of water necessary to fully hydrate and chemically react with the cement ground to a Class G grain size. If too much water is used (to aid in pumping and displacement, for example), lower compressive strength cement and water separation within the cement column will result.
The quality of the water used to mix the cement can vary widely. Fresh water, seawater and some brackish waters are used to mix cement slurries. For any source of water, the setting time and pumpability of the resultant cement must be tested before the slurry is mixed.
Cement Slurry Calculations
The specific gravity of Portland cement compared to water ranges from 3.10 to 3.25 with an average value of 3.14. A sack of Portland Class A-H cement weighs 94 lb, has a bulk volume of 1 (cement plus surrounding air) and absolute volume (only the material) of 3.59 US gal or 0.48
Density of Cement Slurries
The density of a cement slurry is calculated by dividing the sum of the weights of the cement-system (cement, water and additives) by the total of their absolute volumes.
This relationship can then be used to calculate the density of a neat cement slurry for one 94 lb sack of Class A or B cement as follows:
Component | Weight (lb) | Absolute Volume ( ![]() |
---|---|---|
Cement | 94 | 3.59 |
Water | 43.2 | 5.19 |
Total | 137.2 | 8.78 |
Water to Cement Ratio
The water requirement is equal to which represents a water volume of
.
Density of the Slurry =
Notice that the density of the cement slurry is nearly double that of water.
Slurry Yield
Slurry yield is the quantity of slurry that is realized from a single sack of cement, usually measured in cubic foot per sack() or cubic meters per SI ton(
).
For the above example then,
Slurry yield = conversion of
Slurry yield = (generally rounded to
When the volume to be cemented in is known, this relationship can be used to specify the number of sacks of cement required. Or, if the number of sacks of cement required for the job is specified, the slurry volume can be calculated.
Mix water
Another important measurement for a cement job is the total volume of mix water required for the job the gallons of water per sack of cement multiplied by the number of sacks required.
Example:
A cement plan for a 1500 ft intermediate string of casing states “cement with 420 sks of Class H cement”.The yield of Class H cement as shown in Table 1 is 1.18 . Here is how the total required slurry and mix water volumes are calculated:
Slurry volume =
The water/cement mix ratio, as shown in Table 1, is used to calculate the volume of mix water required for the job
Mix water =
Managing BottomHole Pressure during Cementing
During cementing, the pressure at the bottom of the well must be maintained above the pore pressure of the formation, to avoid inflow of formation fluids, and below the fracture pressure to avoid causing a fracture. If the pressure caused by a column of relatively heavy cement slurry is above the fracture pressure, it can be reduced by one of these methods:
- Injecting nitrogen to generate a foamed cement
- Injecting a “lead” lighter cement slurry (for example, Class C cement) that is placed higher up the annular space, followed by a stronger and heavier “tail” cement (for example Class H cement), that is placed at and near the bottom of the casing.