Introduction
When it comes to drilling, the efficiency and safety of operations are of paramount importance. Various factors play a crucial role in achieving optimal drilling outcomes, and one such factor is the Kelly. In this article, we will delve into the concept of Kelly in drilling, its purpose, and its significance in ensuring successful drilling operations. By the end of this article, you will have a comprehensive understanding of what a Kelly is and its role in the drilling process.
What is a Kelly?
A Kelly is a vital component of a rotary drilling system used in the extraction of oil, gas, and other resources from beneath the Earth’s surface. It is a square or hexagonal-shaped steel bar that connects the rotary table to the drill pipe during drilling operations. The Kelly is suspended from the swivel and is responsible for transmitting torque and weight to the drill string.
The Purpose of Kelly in Drilling
The primary purpose of the Kelly is to transfer rotational motion from the rotary table to the drill string. As the rotary table turns the Kelly, it causes the drill string to rotate, enabling the drill bit to penetrate the ground effectively. The Kelly also serves as a conduit for mud flow, facilitating the circulation of drilling fluid down the drill string and back up the annulus to carry cuttings to the surface.
General Description
The kelly is a primary link between the drilling rig’s surface equipment and the bit, and is therefore a critical component of the rotary system. Although top drive systems have replaced kelly/rotary table combinations on many rigs, some knowledge of their manufacture and operation is useful.
Kellys are manufactured with either square or hexagonal cross sections (Figure 1).
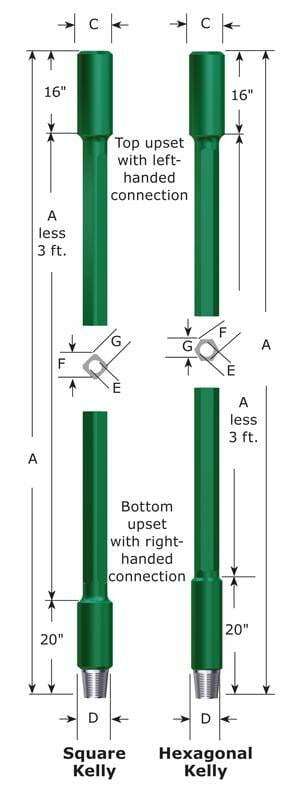
Their angled surfaces, or drive flats, are designed to fit into a drive roller assembly on the kelly bushing, so that as the rotary table turns to the right, the kelly turns with it. To allow for normal right-hand rotation of the drill string, kellys have right-hand threads on their bottom connections and left-hand threads on their top connections.
API Standards
The American Petroleum Institute has established manufacturing and design standards for kellys, and has included them in the follwoing publications:
- API RP 7G, Recommended Practice for Drill Stem Design and Operating Limits.
- API Spec 7-1/ISO 10424-1: Specification for Rotary Drill Stem Elements.
API kellys come in two standard lengths: 40 ft overall, with a 37 ft working space, or 54 ft overall, with a 51 ft working space.
Performance Considerations
For a kelly to be efficient in turning the drill string, the clearance between its drive flat surfaces and the rollers in the kelly bushing must be kept to a minimum. Kellys most often wear out due to a rounding-off of the drive corners, as shown in Figure 1 (new kelly with new drive assembly) and Figure 2 (worn kelly with worn drive assembly).
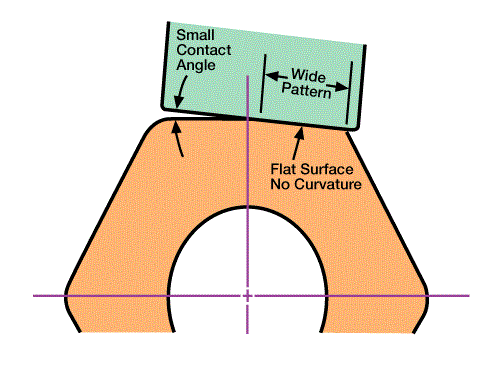
This rounding is a natural wear process caused by the compressive force of the rollers on the drive flats and accelerated by rotary torque.
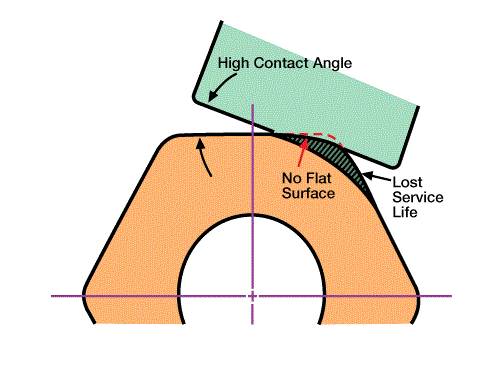
As rounding progresses, it further accelerates the wear process by increasing the clearance and the contact angle between the drive flats and the rollers.
For minimal rounding, there must be a close fit between the kelly and the roller assembly, with the rollers fitting the largest spot on the kelly flats. Manufacturing techniques and rig operating practices play important roles in determining this fit.
Both square and hexagonal kellys are manufactured either from bars with an “as-forged” drive section, or from bars with fully-machined drive sections. Forged kellys are cheaper to manufacture. But machined kellys tend to last longer because:
- Unlike forged kellys, machined kellys are not subject to the metallurgical process of decarburization, which leaves a relatively soft layer of material on the drive surface that can accelerate the rounding process and increase the potential for fatigue cracks;
- Machined kellys are made to closer tolerances than forged kellys,and so are more likely to closely fit the roller assembly throughout their length.
A square drive section normally tolerates a greater clearance between flats and rollers than does a hexagonal drive section.
To minimize rounding, rig personnel should follow these guidelines (Brinegar, 1977):
- Always use new drive-bushing roller assemblies to break in a new kelly.
- If the rollers are adjustable, adjust them to provide minimum clearance.
- Frequently inspect and periodically replace drive assemblies to ensure that clearance and contact angle between the kelly and the rollers is held to a minimum;
- Lubricate drive surfaces to reduce friction and binding at the rollers, and to allow the kelly to slide freely through the kelly bushing.
Fatigue failures are seldom a problem with kellys because of the high-quality steels used in their manufacture. Nevertheless, kellys should be regularly inspected for cracks and other signs of wear, particularly within the threaded connections, in the areas where the flats join the upper and lower upsets and in the center of the drive section.
The areas of highest stress concentration — and therefore the most likely locations for fatigue failure — are the areas where the drive flats join the upper and lower upsets.
In general, the stress level for a given tensile load is less in the drive section of a hexagonal kelly than in the drive section of a square kelly of comparable size. Hexagonal kellys are thus likely to last longer than square kellys before failing under a given bending load.
Kellys can become crooked or bent due to improper handling. Examples of mishandling include dropping the kelly, misaligning it in the rathole and thereby exerting a side pull, using poor tie-down practices during rig moves, not using the kelly scabbard and improper loading or unloading techniques. Depending on where a bend is located, it may cause fatigue damage not only to the kelly but to the rest of the drill string, and can also result in uneven wear on the kelly bushing.
Unusual side motions or swaying of the swivel are good indicators of a crooked kelly. A good field service shop has equipment for straightening bent kellys, making this an easily-corrected problem.
Up to a certain point, a worn kelly can be repaired either by reversing the ends, (Figure 3) or by remachining it to a smaller size.

Auxiliary Equipment
A kelly saver subshould always be run between the kelly and the top joint of drill pipe. This protects the kelly’s lower connection threads from wear, as joints of drill pipe are continually made up and broken out. A saver sub is much less expensive and much easier to replace than the kelly itself, and it can also be equipped with a rubber protector to help keep the kelly centralized and to protect the top joint of casing against wear.
A kelly cock is a valve installed above or below the kelly, which prevents fluid from escaping through the drill string if the well should begin to flow or “kick.” As an extra well control precaution, an upper kelly cock (having left-hand threads) should be installed directly above the kelly, while a lower kelly cock (having right-hand threads) should be installed below the kelly. Installing two kelly cocks ensures that at least one of them is always accessible, regardless of the kelly’s position.
Automatic check valves, designed to close when the mud pumps are shut off, are also available, and can be installed below the kelly to prevent mud from spilling onto the rig floor during connections.
Significance of Kelly in Drilling Operations
Efficient drilling operations require precise control over the drill string’s rotational speed and weight. The Kelly plays a vital role in achieving this control by transmitting torque and weight from the rotary table to the drill string. Proper management of these parameters is crucial for several reasons:
- Drilling Performance: The ability to control the rotational speed and weight of the drill string allows for optimal drilling performance. By adjusting these parameters, drillers can adapt to different formations, increase drilling penetration rates, and enhance overall efficiency.
- Wellbore Stability: Maintaining appropriate torque and weight on the drill string helps stabilize the wellbore. Adequate stability reduces the risk of wellbore collapse, minimizes damage to the drill string, and prevents the loss of drilling fluid.
- Hole Cleaning: The circulation of drilling fluid facilitated by the Kelly is essential for efficient hole cleaning. Proper removal of cuttings and debris from the wellbore enhances drilling efficiency, reduces the chances of stuck pipe, and promotes the overall success of the operation.
- Safety Considerations: The Kelly cock valve and other safety features associated with the Kelly contribute to the overall safety of drilling operations. They help prevent blowouts, control fluid pressures, and safeguard personnel and equipment.