Underbalanced Drilling Techniques
Underbalanced drilling techniques are classified according to density of the fluids used in the process. Typical fluid densities range from near 0 to 7 pounds per gallon.
In fresh-water applications, the density of the circulating fluid can be reduced by nitrogen gas injection. This reduced density helps to achieve a bottom hole circulating pressure that is less than that of the formation pressure.
Even conventional liquids can provide underbalanced conditions with proper density control of the drilling fluid. On the other hand, it is also possible for a low-density fluid to cause overbalance due to the frictional pressure drop.
Underbalanced drilling has proved to be an economical method for drilling in depleted/low pressure reservoirs. Since it is possible to record production during drilling, operators can easily and accurately identify inflow mechanisms and pay intervals, and cease drilling operation as soon as the target zones are identified.
One method of controlling the bottomhole pressure (BHP) is to use a choke at the surface. BHP is controlled by opening or closing the choke to lower or raise the standpipe pressure. Since the speed of a pressure wave through a static fluid column is equal to the speed of sound in the same medium, a lag time is experienced until the choking action at the surfaces reaches bottomhole. Estimating the lag time in a single-phase system is relatively easy, whereas the same calculation in multi-phase systems can be quite complicated.
Instead of using a choke, the BHP can also be controlled by adjusting the Equivalent Circulating Density (ECD). This technique essentially creates an increasing fluid density gradient between the surface and the bottomhole. If the casing is set at a shallower depth, ECD is preferred over choke pressure control. Since ECD is a function of flow, underbalanced conditions should be preserved by controlling the hydrostatic head when flow stops during connections.
The greater the flow resistance, the higher ECD will be. On the other hand, it can also create an opposing condition when pipe is pulled out of the hole, causing a swabbing effect.
Underbalanced Drilling Fluids
There are three primary types of fluids used in underbalanced drilling operations:
- Gaseous (Compressible).
- Two-phase.
- Liquid (Incompressible).
The fluid type is dictated by the boundary conditions of the drilling system. Typically, the boundary conditions are defined by bottomhole flowing pressure, formation fracture pressure, borehole collapse pressure and formation pore pressure. The density range of various drilling fluids is summarized in Figure 1.

Two different measures are used to define the type of fluid system:
- Ratio, the gas-to-liquid volume at standard conditions.
- Quality, the ratio of gas volume to liquid volume at hole conditions.
Gas-to-liquid ratios of various drilling fluid systems are shown in Figure 2.
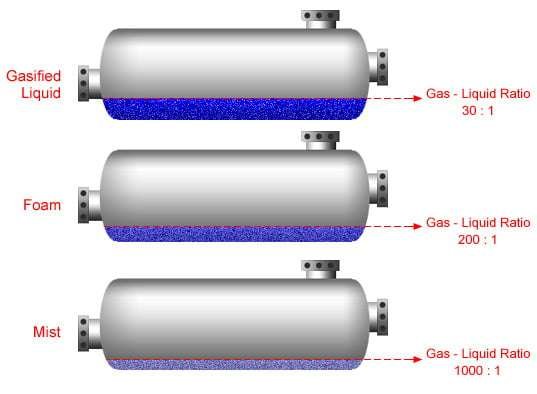
Gaseous Drilling Fluids
The oldest and most basic technique is dry air drilling, which involves pumping air down the drill string and up through the annulus. A rotating wellhead between the blowout preventer and rotary table is used to divert the returns. The cuttings are sent away from the rig via a discharge pipe, and a water spray is used to kill dust at the outlet. A flame is used to burn any returning hydrocarbons.
Nitrogen is another common drilling fluid. Other inert gases are too expensive to be used in this process. A typical method to generate N2 is to use membrane type filters that extract the N2 from the air stream before it is pumped into the wellbore.
Natural gas is also a drilling fluid option, since it is easily available from pipelines. It can directly be used without the help of compressors. More information on nitrogen and natural gas drilling is provided under the “Underbalanced Drilling Methods” subtopic.
Circulating pressure and hole cleanup are dependent on each other. More cuttings in the wellbore cause higher downhole pressures. Angel’s method provides some guidelines regarding air flow rates required for hole cleaning. His charts are still widely used. According to these charts, 3000 ft/min is the minimum velocity for effective cutting transport.
Two-Phase Drilling Fluids
Two-phase drilling fluids, or lightened drilling fluids, consist of either foam-type fluids or aerated drilling mud. Liquids are mixed with gas to achieve a required circulating fluid density. The equation of state method is used to predict fluid properties at downhole conditions.
A pump is used to inject liquid into a gas stream before it enters the well. The small liquid droplets affect the behavior of the circulating gas. If more liquids (2.5% -25%) are introduced, then a foam phase is generated in which the liquid forms a continuous structure, entrapping the gas bubbles inside.
Once the liquid volume exceeds 25%, we no longer have a foam structure. This next level comprises aerated drilling muds (fresh water, brine, diesel or crude oil). Parasite strings are typically used to introduce gas into the circulating liquid stream. A parasite string is an external flow path (possibly coiled tubing), which is run and cemented outside of the casing.
Since gas and liquid compressibility values differ significantly from each other as pressure and temperature changes, the liquid fraction changes as well. Frictional pressure drops are controlled mainly by the flow regime, flow rate, fluid properties and flow geometry. Therefore, phase behavior is a very important component in underbalanced drilling models. Many investigators, including a special institute at the University of Tulsa, have extensively analyzed two-phase flow patterns and regimes. Some of the most common two-phase flow regimes are:
- Bubble flow.
- Annular dispersed flow.
- Stratified or laminar flow.
- Plug or churn flow.
- Slug flow.
Liquid Drilling Fluids
Since formation pressure is usually larger than the hydrostatic pressure of fresh water or saline water, conventional drilling fluids might also provide underbalanced conditions. Even if the drilling fluid density exceeds the formation pore gradient, fluid loss into a formation can cause reduced pressure regions within the wellbore, thus allowing formation fluids to flow in.