Medium Turn Radius Drilling
A medium turn radius well has at least one section with a build rate angle of between 6° and 20° per 100 ft in the rotary mode, and as much as 35° per 100 ft in an oriented mode, in reaching horizontal. The radius of curvature ranges from about 160 up to 1000 feet.
Medium-radius wells are appropriate for areas that could benefit from horizontal drilling, but where long-radius methods are either unnecessary or impractical, as would be the case when lease boundary restrictions limit the well course. They are particularly applicable for re-entry wells sandstone reservoirs, reef reservoirs, fractured reservoirs and reservoirs with potential for gas or water coning.
The primary advantage of medium radius over long radius drilling is that the well profile is shorter. A medium-radius well can reach the lateral section with greater precision at a shallower depth, with less departure from vertical, and in less time than it takes to drill the curved section of a long radius well. Torque and drag tendencies are also less than in long-radius wells. The vertical portion of the well can be drilled deeper and casing set deeper before beginning the directional drilling phase, and upon completion, production equipment can be set in the vertical section, closer to the pay interval.
Relative disadvantages of medium radius drilling are an inability to build angle using rotary methods (however, steerable systems are commercially available that allow an operator to switch from a rotary to an oriented mode without having to trip the drilling assembly), and that fact that the tighter radius places more stress on the drill string. There are no restrictions on bit type or coring capabilities, although MWD applications are limited for hole diameters smaller than about six-and-one eighth inches.
Heavy-wall drill pipe can be used for build rates of up to 15 degrees per 100 feet. Higher build rates require compressive service drill pipe. Figure 1 (Medium radius fixed-angle and steerable angle-build motors) illustrates typical fixed-angle build and steerable angle build assemblies, which allow for continuous, smooth curvature build-up.
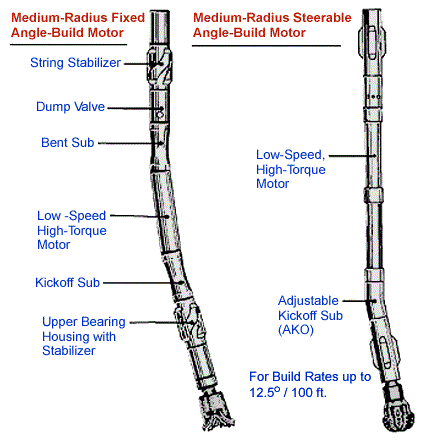
The angle hold assembly may be of the conventional rotary type, or it may contain a downhole motor.
In some cases, an operator may drill a vertical or inclined rat hole for locating, logging and testing the pay zone before drilling the curved portion of the horizontal well. This works to good advantage in identifying the target horizon, especially if the structure is not thoroughly understood or the target zone is very narrow. Where coning is a problem, or in interbedded sands, this is a good way to identify the various gas, water and formation interfaces. Once the target has been defined in this manner, the usual procedure is to plug back the rat hole with a good quality cement plug and prepare to drill the angle build portion of the well.