Connections

In the box connection, the critical zone is just short of the end of the pin at the root of the last engaged thread. It is not supported by the mating pin threads, and it is the weakest section in the box. The critical zone of the pin is about 3/4′′ from the shoulder, at the root of the thread.
Section modulus ratios from 2.25 to 2.75 work very well under most conditions, and in some cases, ratios from 2.0 to 3.2 give satisfactory performance. These numbers for bending fatigue balance are only valid if the connection is properly tightened so that the pin gets sufficient shoulder support.
Torsional strength is another important structural property of rotary-shouldered connections. Critical areas of pin (AP) and box (AB) that are used for torsional strength are also shown in Figure 1. This torsional strength determines the required make-up torque. API RP 7G provides complete torque information for the various sizes of connections and collars.
Drill Collars vs. Drill Pipe
The difference between the treatment and properties of drill collar connections and drill pipe tool joint connections is often misunderstood. A drill collar connection can never be made as strong as the drill collar body. It is a sacrificial element. When it becomes worn, it is cut off and replaced by machining new threads.
Drill pipe tool joint connections, in contrast, are much stiffer and stronger than the pipe body. They seldom experience bending fatigue damage. The most common damage to tool joint threads results from leaking joints, rough handling, thread wear and swelled boxes made thin by outside diameter wear. Damaged tool joints can often be reworked and returned to service by chasing (that is, straightening and cleaning) the threads, thus losing only a fraction of an inch in length.
API Numbered Connections
Historically, the nominal size of a rotary-shouldered connection was the actual outside diameter of the drill pipe that the tool joint was designed to fit. The same connections have been used on drill collars, although the nominal size has no meaning when applied to drill collars. Many old connections have been incorporated into the API Numbered Connection (NC) series.
The numbered connection series provides a good selection of connections for almost any size drill collar. Any other API connection with four threads per inch works well. A thread with a 0.038 inch root radius will have less notch effect than a thread with a smaller radius.
Selection Criteria
Avoid using drill collar connections with five threads per inch. The 90° threads make good drill collar connections, but relative to API threads, recommended make-up torques result in reduced shoulder loads. Higher hoop stresses are developed and thin boxes must be avoided.
Good connections are designed to fit drill collars through 11′′ OD. A problem, however, is that only large rigs may have tongs and line pull capacities to handle a 7 5/8 inch joint that would be used on a 9 or 9 3/4 inch drill collar. Only a very few rigs can handle an 8 5/8 inch connection on a 10 or 11 inch drill collar. There are two methods for alleviating this problem:
- A fishing neck can be used, where the drill collar diameter is reduced for about one foot on the pin end and three feet on the box end (Figure 2).
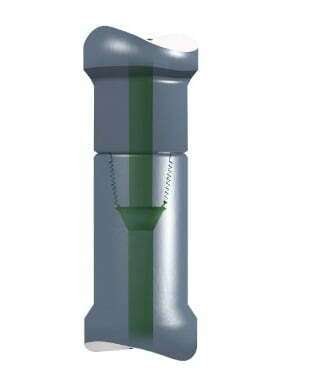
For example, a 9′′ drill collar may be reduced to 8 1/4′′ for a 6 5/8′′ connection, while a 10′′ drill collar may be reduced to 9 5/8′′ for a 7′′ connection.
- A low torque face (Figure 3) may be used.
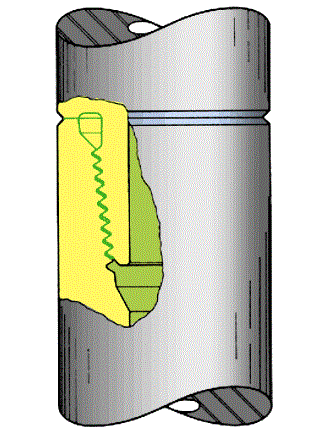
In some cases, a combination of fishing necks and low torque faces may be used. The important thing to remember is that sufficient torque on a modified end or, if necessary, a smaller joint is far better than inadequate torque on a full-size end and a larger joint.
A feature recommended for all drill collars is cold rolling of thread roots. Cold rolling forces metal fibers into compression in the thread root area, making the connection more resistant to bending fatigue. This is standard procedure for most manufacturers. Good repair shops are also equipped to cold roll re-cut drill collars. This process improves resistance to notch fatigue and has not shown any adverse effects. Stress relief features are highly recommended for drill collars, and are almost universally used on drill collars five inches in diameter or larger (Figure 4).
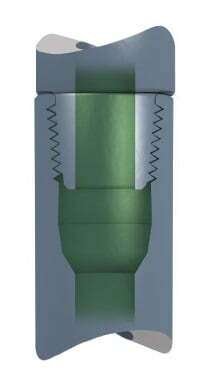
The only disadvantage of these features is that more of the collar must be removed to re-cut a joint. However, a damaged drill collar joint is usually in such poor condition that it is good practice in any event to remove most of the old joint before cutting.
Drill collars smaller than five inches outside diameter are seldom damaged by fatigue. Most damage while in service results from high torque. Drill collars with a 4 3/4 inch OD × 2 inch ID are manufactured about equally with and without relief features. In this case, no set rules apply, and operating conditions dictate the preference.
Stress relief features only slightly reduce the torsional strength of a connection. On medium and large connections, this strength reduction is insignificant — it should, however, be considered on small connections. Collars with a 2 7/8 inch internal flush bore, or smaller joints, should never be supplied with stress relief features.