Transport and Delivery of Basic Elements: Cement, Additives, Water
Transport and Delivery of Cement
Portland cement, the basic component of oil well cement slurry, is usually stored in bulk silos (Figure 1) or sacks (Figure 2) at a central storage location managed by the cementing service company. A standard U.S. sack of API Class A-H cement weighs 94 lbs and contains 1.0 cubic foot of dry cement. A metric sack contains 50 kg (0.033 cubic meters) and is slightly larger than the U.S. sack. There are also 0.5 or 1.5 metric ton “big bags” used for shipping larger volumes of cement.

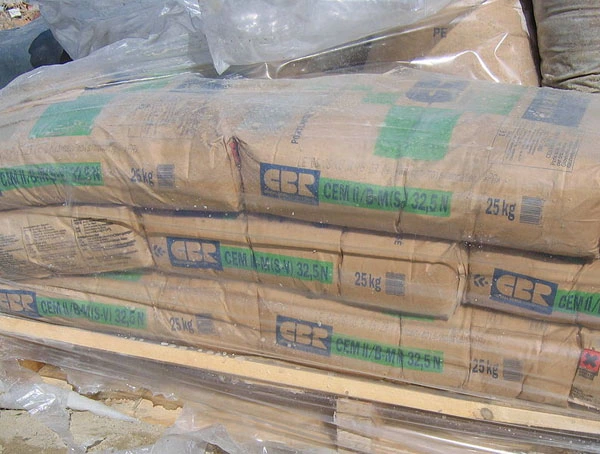
After dry additives are added as needed for a specific job, the bulk cement is delivered to the well site via truck at onshore locations or supply vessel at offshore locations (Figure 3).
Delivery, Storage and Transport of Dry Cement and Additives

2. Bulk (Note the absence of a surge tank on the trailer.)
3. Sacks, large bags, or bulk
4. Pneumatic silo
5. Pneumatic loading bottle
6. Dry-additive blender
7. Air-compressor plant
8. Horizontal tank trailer with merge tank
9. Twin vertical tank trailer with merge tank
10. Supply boat, cementing barge, or vessel
Transport and Storage of Additives
Dry cement additives, if they are not chemically active (for example weighting agents, or powdered coal extender), are typically mixed with the dry cement in a pneumatic blending tank at the central storage location several days before the cement job and then the blended material is transported to the job site.
If the dry additives are chemically active (for example, lignosulfonate retarder, sodium silicate extender, and calcium chloride accelerator) they are normally dry-blended with the cement on location or sometimes added to the mix water in an open horizontal tank immediately before the job.
Liquid additives, all of which are chemically active, are normally water solutions of dry additives. These are often mixed at concentrations up to 3 gal per U.S. sack (up to 25 liters per 100 kg cement). Liquid additives are shipped and stored in liquid tote tanks (Figure 4).
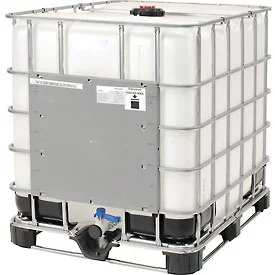
Liquid additives are typically blended with the mix water on location as needed during a job or in a horizontal tank before the job. Because they are blended with the mix water, liquid additive slurries tend to be more homogeneous than those mixed from dry blended powers. Liquid additives are more commonly used offshore because the mixing uses less space. Also, adding liquid additives only as needed reduces the consequences of postponing a cementing job, where storage and reuse of dry mixtures with a shelf life can be problematic.
Figure 5 shows the options for mixing cement and additives. Once at the well location, the dry cement/additive mixture is mixed with the water/additive mixture in the cement mixer before it is sent to the pump(s).

- Usually bulk, possible U.S. (94 lbm) or metric (50 kg) sacks, or “big bags” (0.5 to 1.5 metric tons)
- Manufacturer’s packaging
- Bulk (For very small or unplanned jobs, cement is sometimes stocked in paper sacks.)
- Bulk in special containers, unless mixing is done in an open tank
It is important that the cement slurry that will be pumped be as close as possible to the slurry design tested in the laboratory. Quality control should begin with bulk cement transportation and mixing procedures. Settling during transportation, particle shear as the cement is blown from one vessel to another, or how the mixer in use on location might differ from lab mixers are all factors that should be considered. High humidity in the storage area can cause the cement properties to change. Bulk blending should be rigorously controlled and monitored.
Transport and Storage of Water
Fresh water is normally used for cementing at onshore locations, and seawater is used at offshore locations. Sea water is generally consistent in terms of its ionic components, but fresh water dissolved-solids content can vary from location to location. Organic materials in surface water can also affect the behavior of cement slurries. It is important to test the water and use a representative sample for laboratory testing of the slurry. Similarly, the water storage systems used at the location (such as tanks and trucks) should not introduce contaminants.