Fluid Loss Control Additives
When the pressure exerted by a column of cement slurry exceeds the pore pressure of a permeable formation, water from the cement slurry filters into the formation, leaving solid cement particles behind. If this fluid loss is not controlled, the slurry density increases – possibly to the point that it can no longer be pumped.
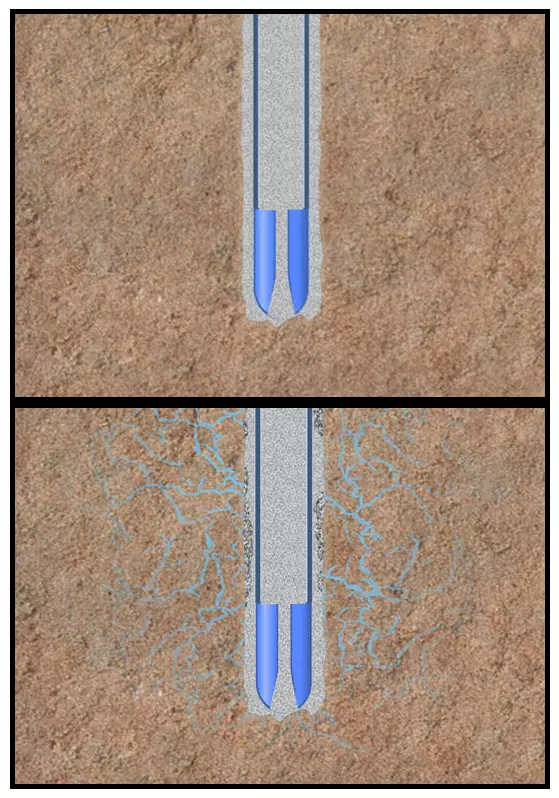
Other related problems can include:
- Casing being pushed against borehole wall
- Decentralization of the casing and differential sticking against the borehole wall
- Filtrate leaking into a productive zone causing formation damage
- Solid cement forming above a gas zone blocking hydrostatic pressure and causing gas influx
Cement slurry fluid loss is measured by a standard API test and expressed in units of volume-per-time. The “API fluid loss” for neat cement slurry is typically greater than . However, a fluid loss range of
is often required to maintain adequate slurry performance, so fluid loss additives are nearly always needed.
There are two classes of fluid loss additives:
- Particulate materials that reduce the cement filter cake permeability.
- Water soluble polymers that increase the viscosity of the aqueous phase.
The first fluid loss control agent for cement was bentonite. Particulate additives also include carbonate powder, carbon black, microsilica, asphaltenes and thermoplastic resins. Another fluid loss additive is based on crosslinked polyvinyl alcohol (PVA) microgels.
Water soluble polymers, first used in drilling fluids in the 1940s, are high molecular weight compounds that can thicken the water significantly depending on polymer concentration. There are two basic categories, natural and synthetic. The most common natural polymers are cellulosic and the most common used as a cement fluid loss agent is hydroxyethylcellulose (HEC). There are also a number of synthetic polymers that include polyvinyl alcohol (PVA), polyacrylamides, and polyethylene imine (PEI).