Weighting Materials (Density-Increasing Additives)
High pore pressures encountered in deep wells or abnormally pressured formations are controlled by increasing the density – and therefore the hydrostatic pressure – of the drilling fluid in the wellbore. To maintain control of these wells during cementing operations, the density of the cement slurry must likewise be increased.
One way to increase the density is to simply decrease the amount of mix water, but this creates other problems and reaches a practical limit at about 18 lbm/gal. Higher densities require adding materials with a high specific gravity. To be effective, these weighting materials must have certain characteristics:
- They must have a particle-size distribution that is compatible with the cement. Particles that are too large will settle out, while particles that are too small will significantly increase the slurry viscosity.
- They must not require additional mix water.
- They must be inert with respect to other additives and the chemical reactions of cement hydration.
Also, the weighted cement slurry must have adequate viscosity and gel strength to carry and suspend these high-specific-gravity solids.
The most common weighting agents are high specific gravity minerals: ilmenite, hematite, barite, and manganese tetraoxide (Figure 1). These are prepared as powders or granules and have specific gravities between 4.3 and 4.95.
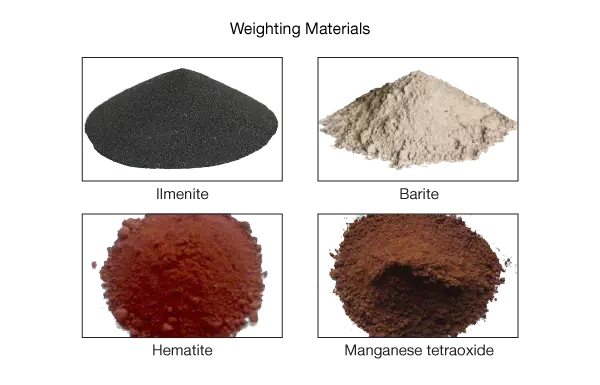
A density of up to 22 can be obtained with hematite or ilmenite plus friction-reducing additives. Barite can achieve densities of up to about 19
but it requires a relatively larger amount of water, which reduces compressive strength and retards thickening time. A 44% BWOC water slurry of Class H cement has a density of about 17.2
, but with a barite concentration of 80% BWOC the density reaches 18
(Figure 2).
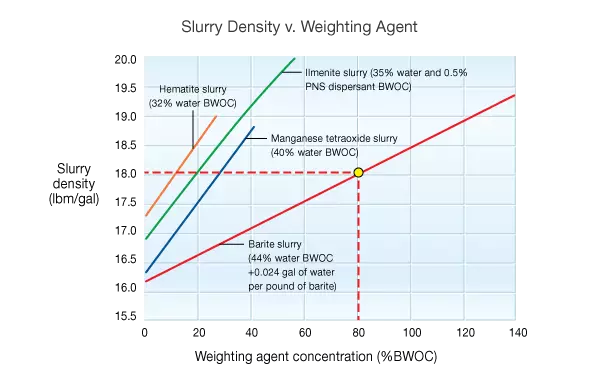