Extenders (Density-Reducing Additives)
Extenders are designed to reduce the density of a cement slurry, and also to increase its yield (volume of set cement produced from a given volume of dry cement). Extenders offer the following benefits:
- A decrease in density reduces the hydrostatic pressure of the cement column in the well, thus reducing the likelihood that it will break down weak formations during the placement process.
- The lower hydrostatic pressure can reduce the number of “stages” needed to cement the well. (Multiple stage cementing is discussed in “Primary Cementing Design and Operations.”) This eliminates the need for special equipment and can reduce the time needed to place the cement.
- Increasing the yield can improve the economics of the cementing operation.
Table 1 lists the three main categories of extenders.
Extender type | Description |
---|---|
Water extenders | Clays such as bentonite and other water-viscosifying agents allow the addition of more water than normal to the slurry while still maintaining homogeneity and preventing the separation of a free water phase. |
Low-density aggregates | These include a variety of materials that have a lower density than Portland cement (3.20 ![]() |
Gaseous extenders | Nitrogen or air can be used to prepare foamed cements, which have very low density but are capable of building compressive strength. |
Water Extenders
The most common extender is bentonite, also known as “gel.” Bentonite is a major component of water-based drilling muds, but “mud gel” should not be substituted for cement-grade bentonite. Additives used to improve the performance of bentonite in drilling fluids make it unsuitable as a cement extender (Grant 1990).
Bentonite is typically added in concentrations between 1% and 16% by weight of cement (BWOC). Above 6%, the addition of a dispersant is usually necessary to reduce the viscosity-increasing and gelling attributes of the clay. Additional water is typically added to the slurry along with the clay. As the percentage of bentonite increases the slurry density decreases and yield increases (Table 2).
% Bentonite | Water (gal/sack) | Slurry Density (lbm/gal) | Yield (ft3/sack) |
---|---|---|---|
0 | 4.97 | 15.8 | 1.14 |
4 | 7.36 | 14.4 | 1.48 |
8 | 9.76 | 13.5 | 1.82 |
12 | 12.15 | 12.7 | 2.16 |
16 | 14.55 | 12.3 | 2.51 |
The use of bentonite can compromise compressive strength. Cement with 12% BWOC bentonite has about half the 24-hour compressive strength of the same cement with 4% BWOC bentonite (Figure 1). Bentonite-extended cements are also less resistant to sulfate containing waters and corrosive formation fluids.
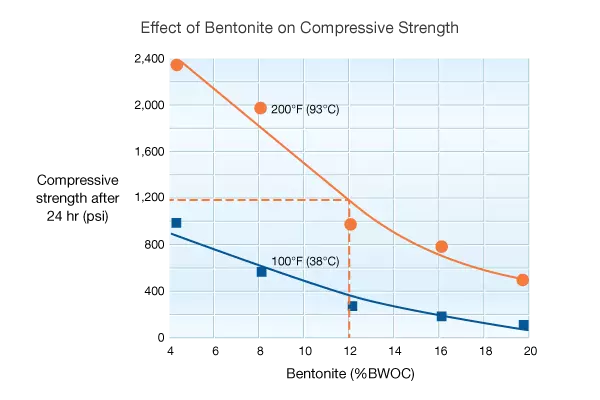
Bentonite may be dry-blended with the cement or prehydrated in the mixing water. In prehydrating, the effect of 1% BWOC prehydrated is approximately equal to 3.5% BWOC dry-blended.
Other water extenders include:
- Sodium meta-silicates that react with lime or calcium chloride in the cement to form a calcium silicate gel and increase viscosity, allowing the addition of extra water.
- Gypsum, the hemihydrate form of calcium sulfate.
- Pozzolans, finely divided siliceous material that extend Portland cement but also react with the calcium hydroxide liberated during the cement hydration process to enhance the compressive strength of the set cement. Examples of pozzolans include volcanic ash, diatomaceous earth, finely divided silica, and power plant fly ash.
Low-Density Aggregates
Low-density aggregates (Figure 2) reduce slurry density because they are lighter than the cement particles. Examples include expanded perlite (crushed volcanic glass expanded via heat), powdered coal, gilsonite (a naturally occurring asphaltic material similar to coal), and glass or ceramic microspheres.
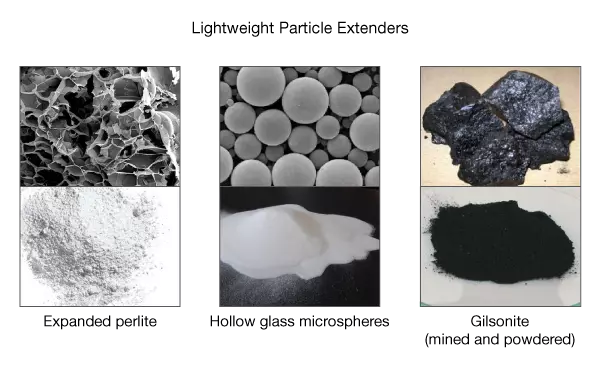
Expanded perlite is a highly buoyant product that requires the concurrent addition of bentonite to prevent separation from the slurry. Because of its low crush strength, the water requirement for perlite-containing slurries must be increased to allow for additional slurry compressibility under downhole conditions.
Gilsonite, a mineral found only in Utah and Colorado, can be used to prepare low density cement systems with relatively high compressive strength. Up to 50 lbm of gilsonite per sack of cement can achieve densities as low as 12 . Gilsonite can plug downhole equipment and bridge across tight annuli, so bentonite is commonly added to prevent bridging in the wellbore.
Powdered coal is sometimes used in the same concentration as gilsonite but the addition of bentonite to prevent separation is normally not required.
Very light slurries (8.5 to 11 ) have been made using hollow glass or ceramic microspheres. These cements are useful for underpressured formations, hot geothermal wells, and other special applications. The synthetic hollow spheres are similar to the natural glass spheres present in fly ash (cenospheres). The primary disadvantage of microspheres is their susceptibility to crushing during mixing and pumping, and when exposed to hydrostatic pressures above crush strength.
Gaseous Extenders
Foamed cement involves the addition of a gas, usually nitrogen or air, directly into the slurry. Densities as low as 3.5 can be achieved (Nelson and Guillot 2006), but this option requires special equipment at the well site to inject the gas and foam generating surfactants into the cement system before it is pumped.
Foams are characterized by their quality, the ratio of the volume occupied by the gas to the total volume of the foam (expressed as a percentage). Good foamed cements consist of nearly spherical bubbles separated by thick liquid films. Qualities are usually less than 50%, and recommended qualities typically range from 18 to 38 percent.
Figure 3 shows cement samples prepared at atmospheric pressure using a Class H cement with a slurry density of 16.5 and four foam qualities: 10%, 20%, 30%, and 40%. Entrained air fractions were mixed using an industry standard foaming agent.
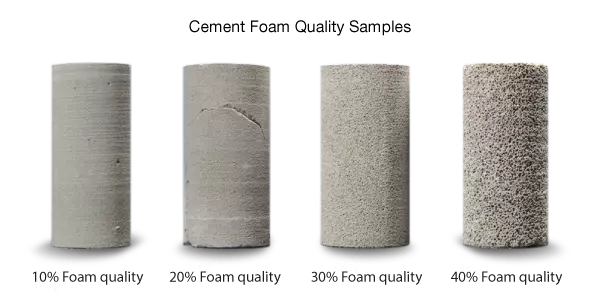