Natural Gas Drilling Overview
Natural gas drilling, like nitrogen, can be used in lieu of dry air to reduce the risk of downhole fires. However, as it is released to the atmosphere, it has a higher potential to create surface fires.
The density of natural gas is generally less than the density of air under the same conditions. Natural gas density is expressed in terms of specific gravity, which is defined as the ratio of the weight of a unit volume of gas to the weight of the same volume of air at standard conditions. Typical natural gas specific gravities are in the range of 0.6 to 0.7. Because of this relatively large density difference, natural gas and air have different cuttings transport efficiencies.
The following equation expresses the cuttings terminal velocity as a function of the drilling fluid density:
Equation 1
where:
vt = terminal velocity, ft/s
dc = particle diameter, ft
ρc = particle density, lbm/ft3
ρf= fluid density, lbm/ft3
CD = drag coefficient
Assuming that the density of the fluid is much less than the density of the cuttings.
Gas gravity is not the only factor that controls downhole pressure. The cuttings concentration is also another factor in determining the gas pressure downhole. Cuttings transport analyses reveal that the gas injection rate required for efficient cuttings transport is higher for natural gas than it is for air. However for the same cuttings transport efficiency, the bottomhole pressure is lower for natural gas compared to air.
Natural gas phase behavior is also more complicated than that of air. It compresses more readily at some pressures compared to an ideal gas. Therefore, in order to produce an accurate model of downhole pressures, the real compressibility of natural gas has to be considered.
Obviously natural gas is more expensive than compressed air. Therefore, hole size becomes an important factor when drilling with natural gas, since it could lead to significant reductions in gas injection rates.
In practice, natural gas drilling can only be conducted if a natural gas supply line is readily available.
Typically a 3 in. line is sufficient to take the gas supply to rig location. Pressure drop calculations must be conducted to estimate the delivery pressure at the wellhead. If the pressure is too low, compressors might be required. Any water or moisture in the supply gas also needs to be removed to reduce the risk of mud ring formation and wellbore stability problems. A typical surface equipment configuration recommended by Cummings (1987) is shown in Figure 1.
Hydrocarbon and hydrogen sulfide detectors need to be installed on the rig site.
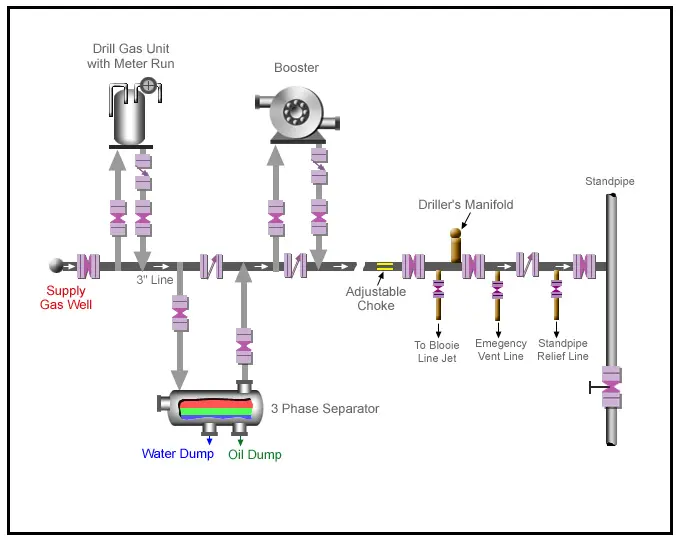
A hydrogen sulfide detector should be also be installed at the blooie line exit.
Large volumes of gas are flared when drilling with natural gas. The design of the flare pit needs to be prepared to accommodate this additional volume requirement. The gas delivery rate is controlled by the choke on the supply line. It is possible to control the gas delivery by following the pressure response at the standpipe. During trips, the drillstring should move away from the rotating head. Then the gas can be directed to the primary jet for flaring.
As in dry air drilling and nitrogen drilling, the formation of mud rings can create problems when drilling with natural gas. When small amounts of water are encountered, the operation must be converted into mist drilling. Since the returning gas is continuously flared, it is important to monitor standpipe pressures to detect water inflow or the formation of mud rings. Sometimes it is possible to observe the change in flare characteristics when significant water inflow occurs.
The biggest limitation to using natural gas as a drilling fluid is its availability near the rig site. Even when there is a natural gas supply close to the rig, cost might become a determining factor in whether to use natural gas for drilling. In some locations, flaring large volumes of gas might not be acceptable because of regulatory and environmental factors.
In the United States, the following safety conformance guidelines must be met when using natural gas on the drilling rig:
- American Petroleum Institute API RP500B: Recommended Practices for Classification of Area for Electrical Installations at Drilling Rigs and Production Facilities on Land and Marine Fixed and Mobile Platforms
- National Fire Protection Association (NFPA) 70: National Electric Code
- NFPA 496: Purged and Pressurized Enclosures for Electrical Equipment in Hazardous (Classified) Locations
Recommended for You