Fatigue and Drill String Failures
It is well known that metal is weaker under dynamic loading than under static conditions. Steel is capable of absorbing dynamic loading, or cycles of stress, for an infinite number of reversals if the stress is kept under a certain limit. This is illustrated in Figure 1—Example of an S-N curve showing stress versus number of cycles to produce failure.
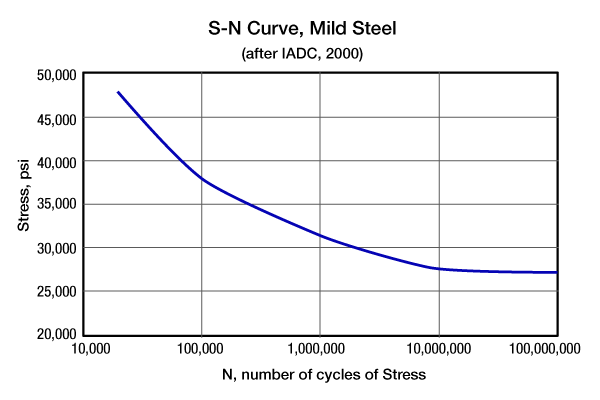
We can use as a simple illustration a nail (mild steel) that is bent back and forth until it breaks.
- The point at which the curve straightens out is called the endurance limit. If the stress does not exceed this limt, the material can undergo any number of cycles without experiencing failure. In this case, if the stress is kept below 27,000 psi the nail will not break regardless of how many times it is bent.
- At 30,000 psi the nail will break after 2,000,000 cycles.
- At 48,000 psi, which is the elastic limit, the nail will break immediately.
These failures that occur under cyclic stress are called fatigue failures.
Fatigue failure is progressive. It starts as a submicroscopic yielding of the atoms along the crystal slip planes. As the metal continues to move under alternating stress, heat is generated, lowering the cohesive strength of the constituents. This forms submicroscopic cracks which progressively unite until the resulting crack becomes visible. The direction of the crack is normal (90 degrees) to the stress— drill pipe failures are thus circumferential.
Some of the properties of steel that determine its endurance limt include chemical composition, microstructure, surface finish, and tensile properties. As a very rough approximation, the fatigue strength of drill pipe is about one half of its tensile strength. In addition, the presence of notches and corrosion have a great effect on the fatigue strength.
Drill pipe is subjected to cyclic stresses in tension, compression, torsion and bending. Tension and bending (alternate tension and compression of the same pipe wall) are the most critical of these stresses. The magnitude of any stress can be compounded by the effect of vibration.
Pure fatigue failures in straight hole drilling—exclusive of dog-legged or deviated holes, or where failures are associated with notches and corrosion—are becoming less frequent. As is discussed in the IPIMS subtopic Drill Collars, this is due to the general practice of using sufficient drill collar weight (accounting for buoyancy and hole inclination) so that the drill string is in tension down through the top two or three drill collars. Today the major factor in fatigue failures is the cyclic bending when pipe is rotated in a hole having a change in direction, or dog-leg. This occurs in straight hole drilling as well as in directional drilling. Failure can occur even when proper drill collar weight is maintained, and there is no permanent set in the drill pipe. When pipe is deflected and rotated, it goes through cycles of stress from tension to compression on each side of the pipe with each rotation. It might be noted that drill pipe rotating at 100 rpm makes 144,000 revolutions per day if left on bottom continually. Hence in just 7 days there could be more than a million stress cycles on the pipe when rotating under conditions creating variable stress.
The portion of the drill string that is most subject to bending is the drill pipe, just above the drill collars. The maximum stress on the drill pipe occurs in the relatively thin pipe wall, from the run-out point of the upset to approximately 20 inches from the tool joint. This change of cross section in the tool joint acts as a vise and becomes the fulcrum of the bending force. If the pipe could bend uniformly throughout its length, stress would be lower and cycles of stress to failure would be higher.
The amount of drill pipe fatigue damage depends upon:
- The tensile load in the pipe at the dog-leg.
- The severity of the dog-leg.
- The number cycles in the dog-leg of each portion of the pipe.
- The dimensions and properties of the pipe.
Methods are available for estimating the cumulative fatigue on joints of pipe that have been rotated through severe doglegs. The method portrayed in Figure 2 (Fatigue damage in gradual doglegs in a non-corrosive environment. Simple device to be used as a guide in analyzing joints suspected of suffering fatigue damage.
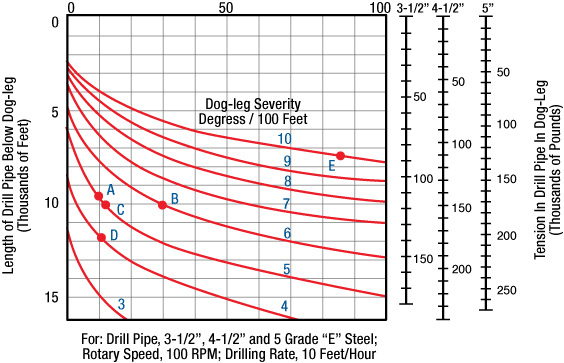
For example, consider a string of 3.5-inch diameter drill pipe under the following conditions:
- Rotary speed = 100 RPM
- Rate of penetration = 100 ft/hr
- Dog-leg severity = 10 degrees per 100 ft
- Length of drill pipe below dog-leg = 6000 ft
- Non-corrosive environment
Based on Figure 2, the tension on the drill pipe would be 70,000 lbf, and the dog-leg would expend about 35 percent of the life of the drill pipe joint.
- Note that such damage is permanent even though the stress is relieved and/or the joint passes through the dog-leg. Similar repetitive stresses on the joint will eventually cause failure. Thus, if the joint passes through this or a similar dog-leg with the same rotary speed and penetration rate three times it will fail.
- In the same regard, drill pipe may be damaged on one hole even though it does not fail. If it is placed near the top of the string on the same or next hole, it may or may not be able to withstand the very nominal bending stresses encountered. Thus, failures can occur later and far from the position in the string where the trouble started, or in subsequent wells.
A correction formula to use for other penetration rates and rotary speed is:
In other words, three times the rotary speed at 1/3 the penetration rate will give the same effect.
If dog-legs of sufficient magnitude are known or suspected, it is good practice to string-ream the dog-leg area. This reduces the severity of the hole angle change.