Cutting and Cleaning Core Plugs and Sidewall Core Samples
Core plug samples, used for a range of different types of core analyses, are often first cut from whole cores as long cylinders, as shown in Figure 1, and then trimmed to create right cylinders, as shown in Figure 2.
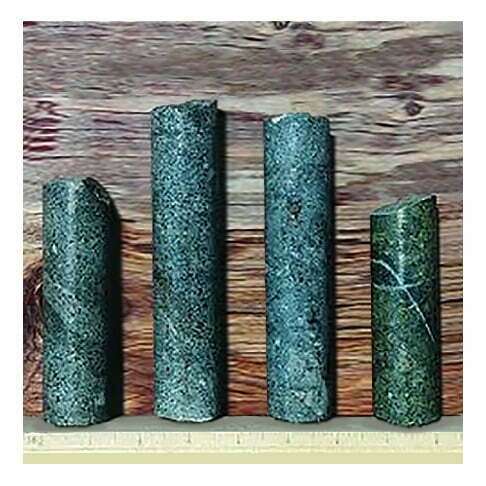
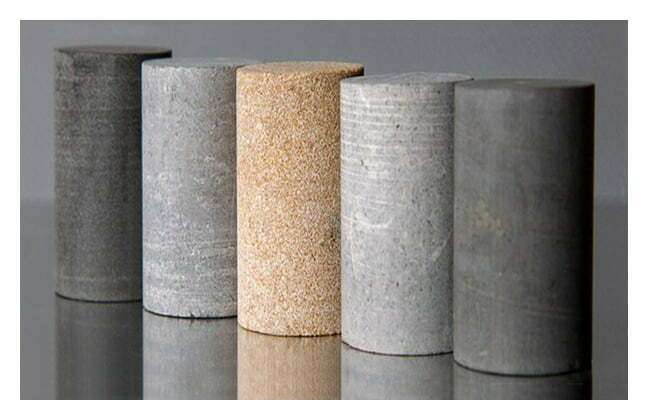
Plug samples are usually cut from a full diameter core with a diamond core bit both parallel and orthogonal to the main bedding planes, and trimmed so as to create a cylindrical plug from the center of the core where the minimum amount of mud filtrate flushing and invasion of drilling mud solids is likely to have occurred. The objective of coring is to recover representative samples of the formation under study. To be fully representative, the samples should not be severely damaged or invaded by non-reservoir fluids. Therefore, sample plugs taken from the center of the core have the highest chance of being the most representative of undisturbed reservoir rock.
Vertical permeability samples are drilled at right angles to the bedding planes, while horizontal permeability samples are cut parallel to the bedding planes. Although primarily used for bedded sandstone reservoirs, this technique is also satisfactory for the more homogenous, non-fractured and non-vuggy carbonates.
The cutting and trimming of such core plugs can affect the subsequent petrophysical measurements. This cutting and trimming process creates “rock flour”, some of which is deposited onto the surface of the core plug. Such a thin layer of debris on the core plug sample tends to have an effect on the subsequent measurements. Remedial techniques have included brushing the core plug dry, brushing it under a liquid, blowing it with air or nitrogen, and conducting the trimming while flowing fluids through the plug ends. These techniques are not universally successful. Brushing may just redistribute the flour into different places on the samples or, even worse, push it deeper into the pore network. Trimming under fluid flow can cause migration of the fines. Some practitioners, as well described by Byrne and Patey in 2004, have returned to a traditional stained acetate peel technique and modified it successfully to remove the vast bulk of the rock flour from both sandstone and carbonate plug end faces and curved surfaces. The acetate peel technique is also used to remove the contaminating layer of debris from preserved or fully saturated samples. Removal of the rock flour creates a fresh and uncontaminated surface that allows more accurate absolute and relative permeability measurements.
Cleaning
In order to conduct the testing and analysis of core samples, they need to be cleaned of residual solids, as shown in Figure 3, and fluids. The cleaning of rock samples can be achieved using many different techniques. For many core analysis measurements, samples are cleaned of pore fluids and contaminants and then measured, either in a dry state or with partial or full re-saturation.
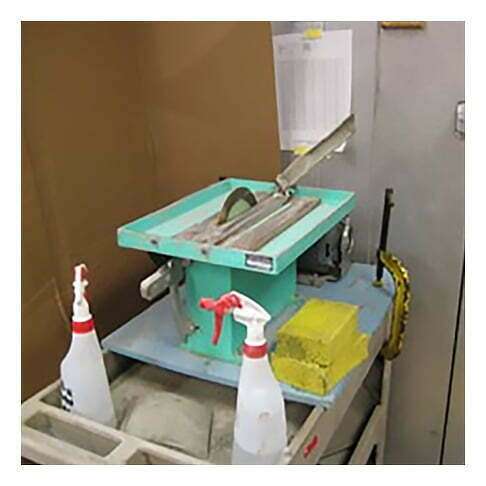
The measurement of permeability and porosity using Boyle’s law, as shown by a graphical representation in Figure 4, and re-saturation techniques requires that the residual fluids be removed, and then the cores be cleaned and dried. The solvents used to remove the oil must not react with the rock or damage delicate minerals such as fibrous clays. Effective solvents include toluene and xylene. Typically, water is removed by heating the rock, with subsequent vaporization, and trapping of the resultant water vapor. Although not part of routine core analysis, samples may be leached with water or methanol to remove any salt left from the vaporized interstitial or filtrate water.
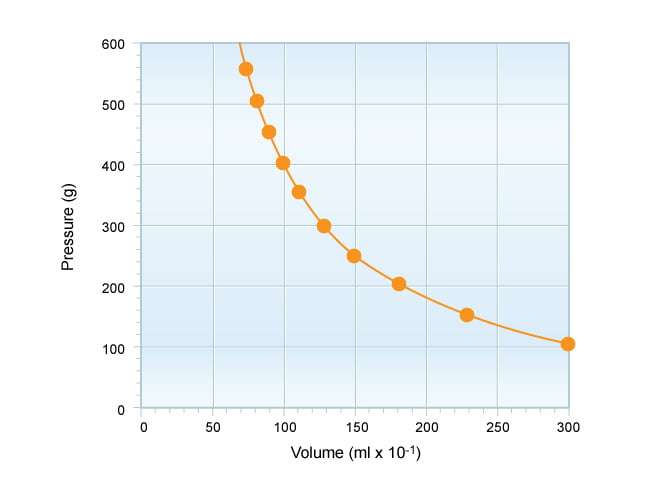
There are several methods for cleaning core samples.
Core Sample Cleaning Methods
1. Cold static cleaning
Cold static cleaning tends to be the least damaging method for cleaning cores; but the very long time required for the process can be a significant issue, as the core analysis results are often required with short deadlines.
2. Soxhlet and Dean-Stark apparatus
Continuous immersion Soxhlet cleaning is one of the best techniques. This method uses a flask wherein the solvent is boiled. The vapor rises and passes into a condenser positioned above the core sample. Condensed solvent drips down into the sample chamber, where it is routed to the chamber base from where it percolates upwards. The chamber is heated and the solvent agitated. Core samples are placed on a perforated shelf placed a few centimeters from the chamber bottom. An outlet at the top of the sample chamber enables the solvent to run off back into the original solvent boiling chamber, allowing the continuous circulation of the solvent. In summary, this process allows the core samples to be in continuous contact with warm, clean liquid solvent, which results in efficient plug cleaning without damaging the delicate minerals.
Refluxing in Dean-Stark or Soxhlet apparatus (Figure 5) is a fairly slow process. The Soxhlet type cleaning should not entail many rapid drying cycles, as the potential damage to the rock core thereby may be unacceptable.
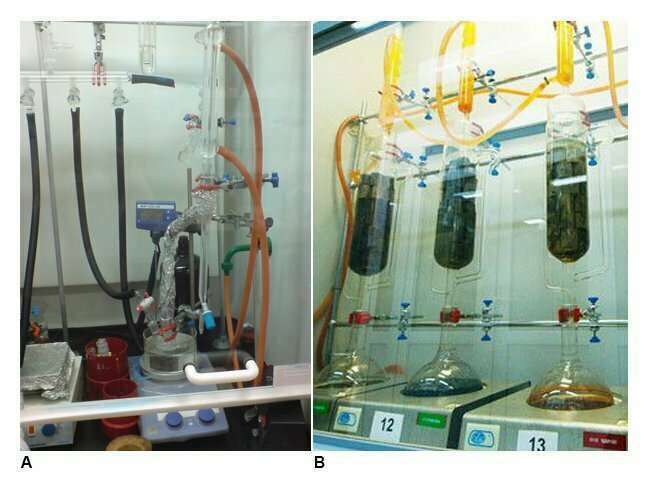
3. Centrifugal flushing
Flushing in a centrifuge, as shown in Figure 6, is limited to plug-size cores and requires that the mechanical strength of the core be sufficient to withstand the centrifugal forces.
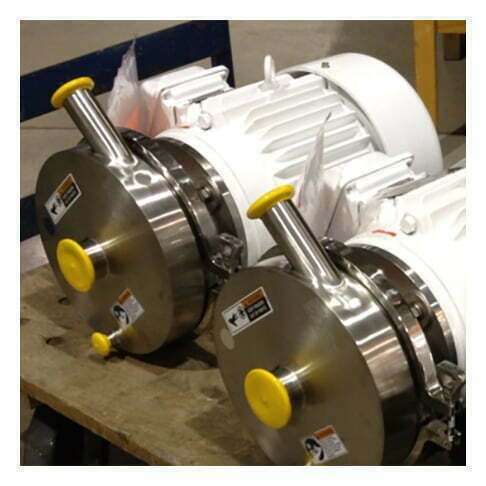
4. Pressure flushing
Equipment for pressure flushing of solvent through the core is shown in Figure 7. This apparatus is a core cleaning system based on controlled sequential solvent displacement under moderate pressure. Extraction of the hydrocarbons and salts from formation rocks is achieved by injecting one or more solvents into the core sample under pressure and moderate temperature. The amount of pressure applied depends on the sample permeability. The core is considered clean when the effluent is clean.
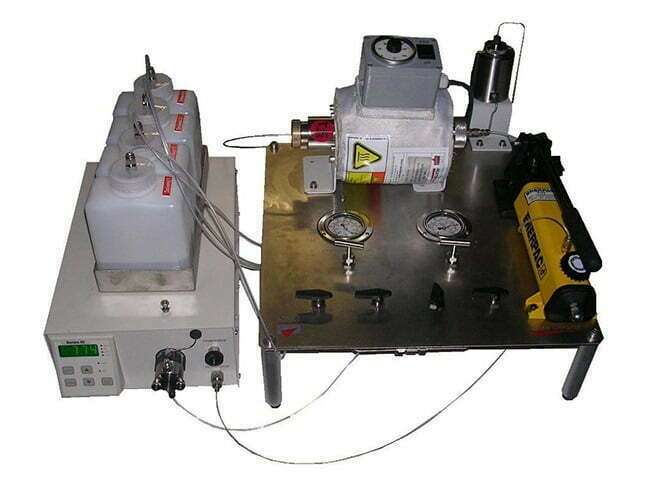
5. Repeated pressure cycling with CO2 and toluene
Repeated pressure cycling of the core with a carbon dioxide and toluene mixture is a relatively fast process (not suitable for poorly consolidated sand or chalky limestone, but a good technique for full diameter cores). Figure 8 shows a typical computer-controlled system designed to clean plug size and full diameter core samples with CO2 saturated toluene in programmed cycles to remove the residual hydrocarbons. The system normally includes a stainless steel core cleaning pressure chamber capable of accommodating core samples up to 4 1/2″ in diameter. Computer software controls the cleaning process and monitors the temperature and pressure of the system.
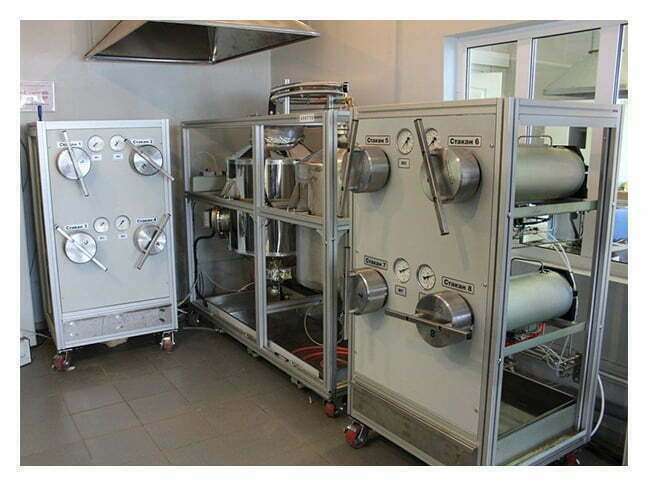
6. Vapor soaking
Vapor soaking, with condensed toluene dripping on the core is more applicable for non-clay and non-gypsum bearing formations.