Downhole Mud Motors
Downhole motors (commonly known as mud motors because they are hydraulically driven by the circulating drilling fluid as it moves down the drill string) have played an integral role in the advancement of directional drilling technology, and in “straight hole” drilling as well. The flexibility and control that they provide is far beyond that attainable with other wellbore deflection techniques, and their use has become prevalent in an ever-widening range of applications, including slim hole and coiled tubing operations.
The distinguishing feature of downhole motors is that they are designed to turn the bit without rotating the drill string. Thus, it’s possible to orient the bit in a desired direction, and maintain it in this direction throughout the bit run. Moreover, drilling in this “oriented” mode reduces the rig’s power requirements and reduces wear on both surface equipment and tubulars.
Downhole motors come in two basic types: positive displacement motors (PDMs) and turbine motors.
Positive Displacement Motors
The positive displacement motor is easily the most versatile tool for building or maintaining hole angle, or for minimizing crooked hole tendencies. It can be run with a bent sub or eccentric stabilizer to initiate deflection. Or, in “crooked hole” formations, it can be run without these accessories as a deviation control tool.
For maximum directional control with a minimum of trip time, we may use a motor with a bent housing. Figure 1 (Steerable positive displacement motor) illustrates a motor in which the bent housing is adjustable.

The heart of the positive displacement motor is the rotor-stator assembly (Figure 2), consisting of a helicoidal rotor that moves within a molded, elastomer-lined stator.

When circulating fluid is forced through this assembly, it imparts torque to the rotor, causing it to turn eccentrically. A universal connection transfers this rotation through a bearing and drive-shaft assembly to a rotating bit sub, which turns the bit.
Positive displacement motors provide excellent steerability for deflecting or straightening the well course. In addition, they allow for increasing the bit RPM without increasing the drill string rotation, and for drilling with less weight-on-bit. This can result in higher penetration rates compared to drilling with a rotating kelly, along with reduced drill pipe and casing wear – an important consideration, especially when drilling high-angle holes.
Positive displacement motors are available in a wide variety of sizes, rotating speeds, rotor/stator configurations and output characteristics, for a broad range of downhole conditions .
Turbine Motors
A turbine motor (Figure 3) consists of multiple rotor/stator assemblies, which drive main thrust-bearing sections.
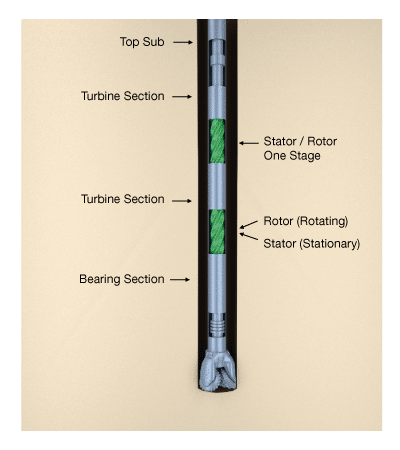
Turbine motors operate at relatively high rotary speeds, and so are run exclusively with fixed cutter (PDC or natural diamond) bits. Some operators see this as an advantage in certain situations, in that these characteristics may help eliminate “bit walk” to the right, allow for higher bit weight (and thus improved drilling rates) and a smoother hole for logging and casing operations than a PDM would provide (von Flatern, 1991).
Turbine motors have narrower operating ranges than positive displacement motors. The relatively small diameter of the turbines and resulting higher rotational speeds translate into greater fluid flow requirements. They also tend to be longer than PDMs, which limits their ability to make high-angle directional changes. Because of these limitations, which are inherent in the turbine motor design, positive displacement motors are used much more commonly.
The operator and directional service company representative should consider the following basic information when selecting a downhole motor (von Flatern, 1991):
- Depths (kickoff point, target, etc.)
- Hole size
- Formation hardness
- Faulting
- Build rate
- Bottomhole temperature
- Conditions at the kickoff point (e.g., inside casing, sidetrack plug, etc.)
- Hydraulics program
- Mud program
- Rig pump capabilities