Vibration Dampeners
One of the more important considerations in drill string design is dealing with the vibrations and shock loads that are produced as the bit rotates on bottom. Such vibrations can cause rough running at the surface, and can result in damage to the bit, drill collars, drill pipe and other components.
There are a number of drilling parameters that determine whether vibration will occur, including:
- formation lithology (e.g., hard rock, broken formations, and formations with intermittent hard and soft streaks)
- depth;
- bottomhole assembly configuration;
- weight on bit
- rotary speed.
Engineers can use these and other parameters during the well planning process to develop computer models for optimizing drill string design. They can also monitor vibrations during the drilling of the well by means of surface or downhole (MWD) sensors. It is often possible to control or eliminate downhole vibrations by modifying the bottomhole assembly configuration, or simply by adjusting rotary speed and/or weight on bit.
A vibration dampener or shock sub may be useful in some cases for absorbing vibrations and shock loads. A vibration dampener is a type of shock absorber designed to prevent vibrations generated by the bit from traveling up the drill string to the surface. It is commonly run between the bit and the drill collars, or above the large-diameter short drill collar segment of a packed-hole drilling assembly. When properly used, vibration dampeners can result in faster drilling rates, longer bit life, less damage to the drill string and surface equipment, and reduced torsional impact.
In its simplest form, a shock sub consists of three parts: a grooved female housing, a matching splined male housing and a set of entrapped spring elements (Figure 1, Figure 2, and Figure 3). The spring and spline mechanisms are lubricated in hydraulic oil which is retained by seals between the housing and the mandrel. When installed above the bit, weight on bit tends to compress the springs and close the shock sub. The pressure drop through the bit nozzles below the tool tends to counteract this by acting against the internal cross section and pumping the tool open. In theory as the bit bounces and or the assembly vibrates the shock sub strokes rapidly up or down around a median point, minimizing fluctuations in WOB and isolating the bit and assembly from each other. Shock subs are used to minimize the effect of drillstring vibrations upon the bit to enhance bit performance and bit life. In addition the effects of bit bounce are reduced and isolated from the drillstring to reduce fatigue wear of the string.
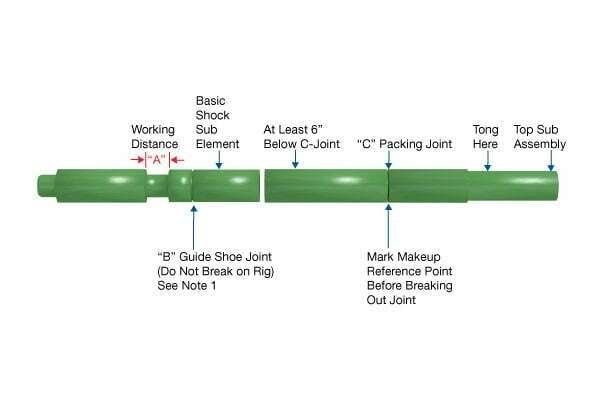
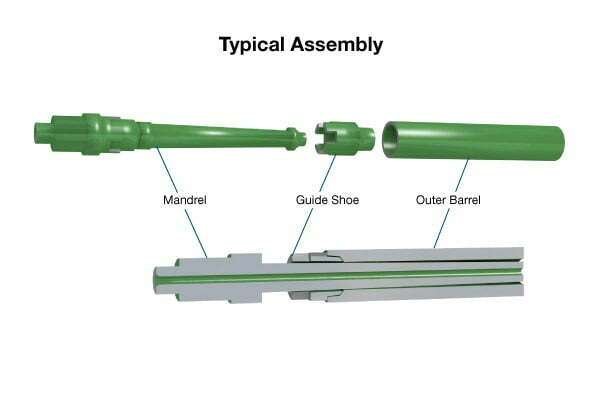

Because of the complexity and magnitude of the forces acting on the bit and drill string, vibration dampeners cannot be considered a cure-all for vibration problems. They should not be routinely added to drill strings without first modeling their effects. Improperly applied, a shock sub may not only fail to absorb severe vibrations, but could even create additional vibrations, thereby accelerating, rather than preventing, drill string failure.