Surfactants
Surfactants, or surface-active agents, lower surface tension by adsorbing at the interface between liquid and gas. Surfactants can also lower interfacial tension by adsorbing at interfaces between two immiscible liquids and changing contact angles by adsorbing at an interface between a liquid and solid. They are commonly used in acidizing (and other completion and workover operations) to demulsify spent acid and oil, reduce interfacial tension, speed cleanup and prevent sludge formation.
Surfactants should not be added to treatment fluids without first having a full understanding of their effects on the reservoir oil at downhole conditions. Without this understanding, it is better not to use surfactants at all in the formulation, particularly when the objective is to break or prevent emulsion (Schecter, 1992).
Surface tension is a property of liquids that distinguishes them from gases. Liquid molecules exert a mutual attractive force on each other. When this force a combination of van der Waals’ forces and electrostatic forces is not balanced, a tension perpendicular to the surface develops. The greater the attractive force of these molecules for one another, the greater the surface tension of the liquid, and the greater the amount of work per unit area required to rupture the liquid surface. This amount of work (surface tension) is specific for each liquid at a definite temperature and is expressed in .
Interfacial tension is the force in the interface, or boundary layer, between two unlike liquids. This tension results from unbalanced intermolecular forces in the boundary region, is a factor in the formation or breaking of emulsions in the recovery of treating fluids from matrix permeability.
In general, surfactants can be divided into four main groups: cationic, anionic, nonionic, and amphoteric.
Cationic surfactants are organic chemicals with molecules that ionize upon contacting water. The water-soluble group is positively charged. The positively charged particle, consisting of oil-soluble and water-soluble ends, contains the surface-active portion of the molecule. The active part orients itself at the liquid/air, acid/oil, or liquid/liquid interface. Most cationic surfactants are amine compounds, such as quaternary ammonium chloride:

where R represents an oil-soluble group.
Anionic surfactants are organic chemicals with molecules that also ionize upon contacting water. But here the negatively charged particle of each ion, consisting of a water-soluble end and an oil-soluble end, is surface active. The anionic surfactant is negatively charged; it is this part that is active in orienting itself at the surface of the liquid, or at the interface between the water and oil. The positively charged particle goes off into solution and has little to do with surface tension.
Some examples of anionic surfactants are:
sulfates
sulfonates
phosphates
phosphonates
where R represents an oil-soluble group.
Of these, the most common anionic surfactants are sulfates and sulfonates. Anionic surfactants are primarily used as nonemulsifying agents, retarding agents, and cleaning agents.
Surfactants are organic molecules that do not ionize and therefore remain uncharged. Most nonionic surfactants contain water groups that are polymers of either ethylene oxide or propylene oxide.
Some examples of nonionic surfactants are:
polyethylene oxide
polypropylene oxide :
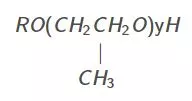
Nonionic surfactants are primarily used as foaming agents and nonemulsifiers.
Amphoteric surfactants are organic molecules with water-soluble groups which can be positively charged, negatively charged, or uncharged. The specific charge depends on system pH level. If the pH is acidic, the amphoteric surfactant takes on cationic properties, or a positive charge. If the pH is in the neutral range, then it takes on nonionic properties, or remains uncharged. If the pH level is basic, the amphoteric takes on anionic negative charge properties.
Two examples of amphoteric surfactants are:
amine sulfonate
amine phosphate
Some amphoteric surfactants are used as corrosion inhibitors, foamers, and silt-suspending agents.
Properties Affected by Surfactants The main fluid properties affected by surfactants are surface and interfacial tensions, emulsification tendency, wettability, and dispersibility.
- Surface Tension: Figure 1 illustrates how surfactants lower surface tension.
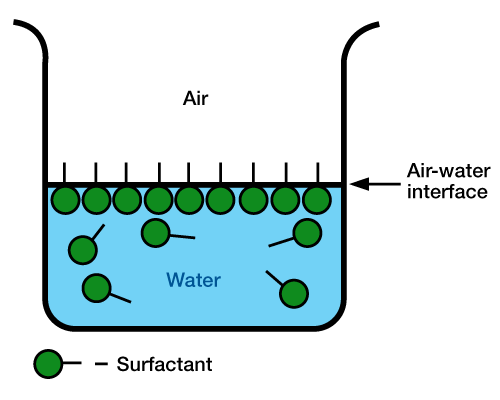
- Since the water-soluble group exceeds the water solubility of the oil-soluble group, surfactant molecules orient themselves at the air/water interface (surface). The water-soluble group is in water, and the oil-soluble group in the air. This changes the nature of the air/water interface, making it a combination of air, water, and oil. Because oil has a much lower surface tension than water, surface tension of the water surfactant mixture is lower than the surface tension of pure water.
Surface tensions of some common liquids are listed in Table 1 (below)
Liquid | Surface Tension![]() |
---|---|
Water | 72.0 |
15% HCL | 72.0 |
Spent 15% HCl | 76.9 |
Octane | 21.8 |
Some surfactants can reduce surface tension of water to about 27 when used in relatively low concentrations. One class of surfactants, called fluoro-surfactants, can lower surface tension below 15
.
- Interfacial Tension: Interfacial tension describes the surface energy between two immiscible fluids, such as water and oil. This interface acts like an invisible membrane that prevents the liquids from mixing. The force required to break this molecular film is called interfacial tension.
The interfacial tension between kerosene and water is about 49 . By the addition of a surfactant, it can be lowered to near zero. Figure 2 (surfactants lower interfacial tension) shows the surfactant being adsorbed at the oil-water interface.
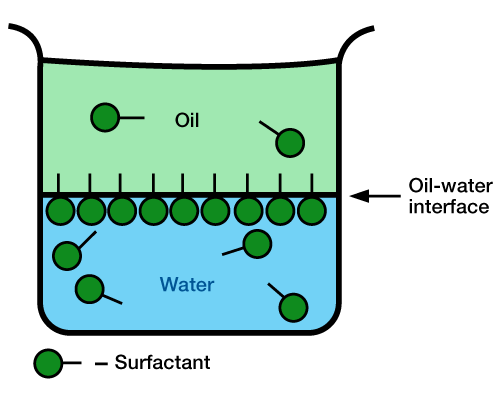
Again, the water-soluble group adheres to the water, and the oil-soluble group is in the oil phase. The interfacial surface between the two fluids is now a mixture of oil and water, with the interfacial tension being greatly reduced. Even though the surfactant is water soluble, some of it migrates through the interface and enters the oil phase.
When interfacial tension is lowered in an acidizing treatment, the water may break up into smaller droplets that pass through the oil and flow out of the well without forming unwanted emulsions. In the case of oil, interfacial tension can be reduced to enable the oil to pass through rock pore spaces with greater ease.
- Emulsification Tendency: An emulsion is a mixture of two fluids in which fine droplets of one fluid remain suspended in the other. Emulsions may be oil-external or water-external. In the first instance, oil is the external phase with the water droplets dispersed throughout. This is the most common emulsion found in wellbores connected to oil reservoirs. Water-external emulsion has an aqueous external phase with oil droplets distributed throughout.
Many crudes contain naturally occurring surfactants that reduce surface tension between oil and formation water and thus promote the development of emulsions. Treatment of the formation with certain surfactants can also lead to the development of emulsions. However, certain surfactants can be used to treat wells with emulsions problems.
- Wettability Oil and water are immiscible liquids that compete for a place on the formation surface. The questions of which liquid preferentially wets the rock surface is an important factor in acidizing. When the formation surface is completely covered by a film of oil, the formation is termed oil-wet. Conversely, when covered by water, the formation is water-wet.
The electrochemical approach usually explains the ability of a surfactant to adsorb at interfaces between liquids and solids and alter the wettability of solids. Most formations are mixtures of sand, clay, limestone, and dolomite. We next consider each of these components.
Sand usually has a negative surface charge. When a cationic surfactant is used, the positive water-soluble group is adsorbed by the negative silica particle. This leaves the oil-soluble group to influence wettability. As a result, cationic surfactants generally oil-wet sand. When anionic surfactants are used, the sand and silicate minerals are generally left in their natural water-wet state. Wettability characteristics exhibited by anionic and cat ionic surfactants on a silicate particle are shown in Figure 3 and Figure 4.
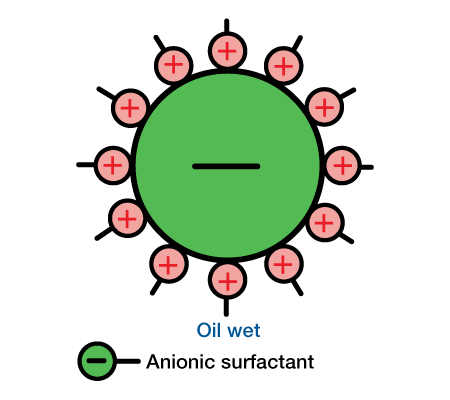
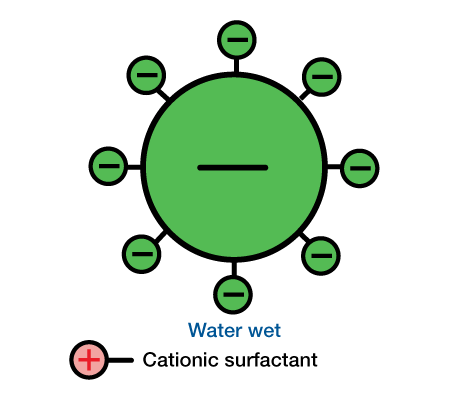
Limestone and dolomite usually have a positive surface charge. Since anionic surfactants have a negative charge, the oil-soluble group is usually left to influence wettability. Hence, anionic surfactants tend to oil-wet lime-stone and dolomite formations.
Because carbonates do not usually adsorb cationic surfactants, most cationic surfactants leave limestone and dolomite in a natural water-wet condition. Wettability characteristics exhibited by anionic and cationic surfactants on a carbonate particle are illustrated in Figure 5 and Figure 6.

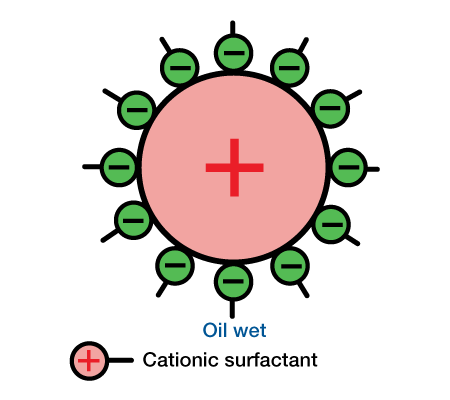
In the case of nonionic surfactants, the wettability of silicates and carbonates depends primarily on the solubility of the material. If the nonionic is oil-soluble, it will tend to oil-wet the silicates. This is because silicates are attracted by hydrogen bonding.
Contact angles are used to study wetting of surfactants. Figure 7 and Figure 8 shows how a wetting and nonwetting drop looks on a solid surface.
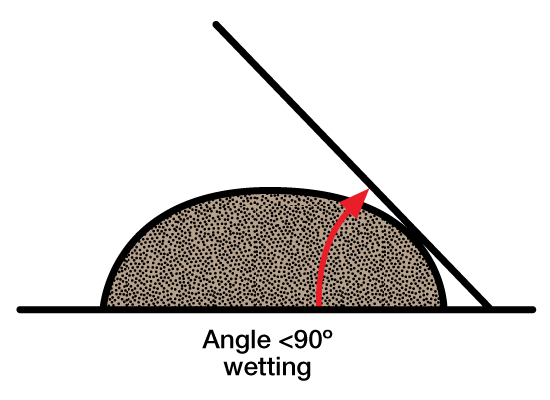
By using the proper surfactant, formation wettability can be changed from oil-wet to water-wet, and vice versa. Since oil flows more easily through water-wet formations, selection of the proper surfactant can be an important factor in increasing oil production.

Figure 9 shows the results of oil flow through oil-wet and water-wet sands.
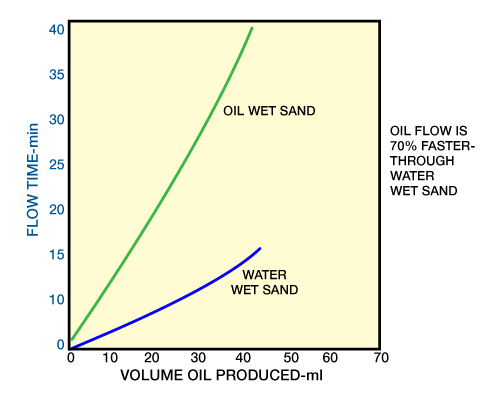
As discussed earlier, certain surfactants are used to alter wetting properties of a producing formation. These curves show that oil exhibits better flow rates through water-wet formations. Care should be taken to have the formation in a water-wet condition following an acidizing treatment, which is often not a simple task. In many instances a surfactant may have been added as an emulsion breaker, and it inadvertently acts as an oil wetter.
- Dispersibility: Surfactants have been developed to inhibit the swelling, migration, and flocculation of clays, even in high ionic strength solutions, such as acids. This is done by using an anionic surfactant which effectively disperses clay particles in acid mud removal solutions and minimizes the formation of aggregates. Since the smaller particles are easier to suspend, the clay is removed more efficiently.
Another system for removing drilling mud is an aqueous solution of surfactants and other chemicals that reduces mud viscosity and disperses solids.
Retarding Agents
These surfactants are designed to slow the reaction time of acid on carbonate formations. Reaction time is the amount of time it takes for acid to spend from its original concentration to a concentration of about 3.2% at conditions of bottomhole temperature and pressure. During matrix or fracture acidizing, or the pumping of large volumes of acid into a carbonate formation, it is sometimes desirable to control the reaction time of the acid.
The principal surfactants used as retarding agents are anionic oil-wetting surfactants, usually sulfonates or sulfates. These function by adsorbing onto the carbonate formation and making part of it oil-wet. Where the surfactant adsorbs most, the acid reacts least. Consequently, an uneven surface is etched into the fracture faces. These uneven surfaces prop the fracture upon completion, resulting in an improved fracture permeability and increased oil and gas production. Cores etched under simulated reservoir conditions: Figure 10 (regular 15% HCl)
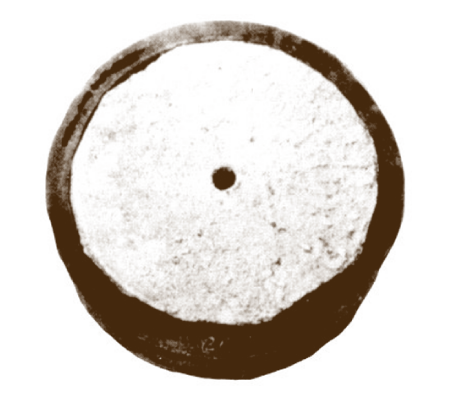
and Figure 11 (acid retarded with anionic surfactant) shows this uneven etching of the acid retarded with an anionic surfactant.

Unfortunately, these additives have proven only marginally beneficial in retarding acid reaction rates in the field, and there use is not generally recommended.
Emulsifying Surfactants
These types of surfactants form with acid either an oil-external emulsion or an acid-external emulsion. The acid-external emulsion is commonly used with a mixture of an aromatic and acid to form a dispersion. The solvent phase in this blend dissolves organic residues, while the acid reacts with scale to remove deposits on the formation to increase permeability.
The high-viscosity oil-external emulsions are more commonly used in fracture acidizing. As the acid spends itself on the formation, the emulsion breaks. The emulsion retards the acid formation reaction by physically preventing acid contact.
Suspending Agents
All calcareous formations less than 100% carbonate. Thus many insoluble fines are released during acidizing. When the spent acid is removed from the formation, these fines can be left behind to reduce permeability.
Two basic types of suspending agents are used in this application. One is a surfactant that adsorbs onto these fines and keeps them in suspension by electrostatic repulsion. The other is a polymer that creates a molecular bridging effect and, by trapping the fines between polymers, keeps fines suspended. Suspending agents are effective when acidizing a carbonate formation that contains HCl-insoluble materials, such as feldspar, quartz, and clays.
Antisludging Agents
When acid contacts some crude oils, a sludge can form at the acid/oil interface. This usually happens when the crude contains a high percentage of asphaltenes, and is most severe with high-strength acid systems (20% or higher). Once formed, the sludge is very difficult to dissolve into oil again. As a result, it accumulates in the formation and decreases permeability.
To combat formation sludge, surfactants, both cationic and anionic, are used to adsorb and provide a continuous layer of protection at the acid/oil interface. Sludge development can also be prevented by lowering acid strength and controlling return rates after an acid treatment. Figure 12 (acid droplet in sludge-forming oil- a skin like precipitate forms around the acid droplet)
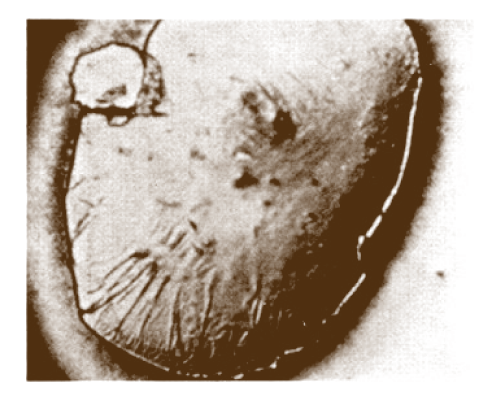
and Figure 13 (acid droplet containing anti-sludge forming oil- no precipitate forms around the acid droplet) illustrate the effectiveness of an antisludging agent.

Penetrating Agents
These surfactants are commonly used in acidizing tight gas reservoirs and in scale-removal treatments. Their main function is to lower surface and interfacial tensions of the acid. This allows the acid to more easily wet the formation rock and oil-wet scales, resulting in a more uniform reaction.
Another benefit of lowering the surface tension of the treating fluid is to decrease the fluid’s likelihood to form water blocks in the formation, resulting in a faster and more efficient cleanup after acidizing.
Most penetrating agents are nonionic surfactants which water-wet both silicates and carbonates. These surfactants effectively lower the surface tension of acid from 72 to about 27
when used in a concentration of 0.1%.
Nonemulsifiers
One major problem encountered in acidizing is emulsification of crude oil and acid, or of crude oil and spent acid. This phenomenon may or may not occur in the formation but does occur in the wellbore. There are two fundamental types of emulsion: oil-external and water-external.
Oil-external emulsion is commonly encountered in oil wells. It is usually a thick, viscous fluid mixture which can reduce the flow rate of the well by plugging the formation. Addition of proper surfactants to the acid before pumping can prevent formation of an emulsion during the acid treatment. Obviously, the selected surfactant must be compatible with acid, formation fluids, and all other additives in the treatment design.
Alcohol
Alcohols are ordinarily used in acidizing fluids to remove water blocks, enhance fluid recovery, retard acid reactivity, and decrease water content. Their effectiveness is limited. The most common alcohols used in acidizing are isopropanol and methanol. Their physical and chemical properties are listed in Table 2.
Properties | Isopropanol | Methanol |
---|---|---|
Specific Gravity at 68 °F | 0.785 | 0.792 |
Flash Point (closed cup) °F | 53.6 | 53.6 |
Solubility in Water | Completely | Completely |
Isopropanol is normally used at a maximum of 20% by volume. Methanol is used at various concentrations, commonly 30% by volume. In some cases, methanol alone is used to dilute concentrated acid to various acid-treating solutions.
Alcohols are used in acidizing fluids for the following reasons:
- Removal of Water Blocks: One problem which can severely decrease production in producing wells is blockage of the pore spaces by water — commonly known as a water block. Water blocks may form where high capillary forces are present in porous rocks. The most severe water-block problems occur in formations with gas permeabilities less than 120 md. The alcohol in the treating fluid reduces the capillary forces within the reservoir, thus permitting easier removal of the liquid phases.
- Enhancement of Fluid Recovery: Another problem encountered in treating oil or gas wells is the recovery of treating fluids, especially in gas reservoirs. The high surface tension of water or acid solution hinders their penetration and recovery. Conventional surfactants help somewhat, although they surfactants lose much of their surface activity by adsorption. The addition of alcohol to acid solutions reduces their surface tension. The concentration of alcohol normally used for this purpose is of sufficient quantity that adsorption is not a problem. Alcohol used in acidizing fluids also increases the vaporization rate of the fluid. This, in turn, lowers vapor pressure, allowing for a more rapid desaturation of water from a gas reservoir.
- Retardation of Acid Reactivity: Alcohol has a retarding effect on acid reactivity. The retardation rate is proportional to the type and percentage of alcohol added.
- Decrease of Water in Acid: Some formations contain a large amount of water-sensitive clays. To minimize the amount of water contained in acidizing solutions, alcohols are used in place of part or all of the dilution water.
The major disadvantages of using alcohol in acidizing fluids are:
- Effective Concentration: It takes a large amount of alcohol, 20% or more, to provide beneficial effects.
- Cost: Replacing water with alcohol in the acidizing solution makes the treatment more expensive.
- Low Flash Point: Both isopropanol and methanol, and even acid solutions containing 20% or more by volume of either, have low flash points.
- Increase in Corrosiveness: Corrosion tests have shown that alcohol-acid mixtures require a higher concentration of inhibitor than equivalent nonalcohol-acid mixtures.
- Adverse Reactions: Formation brines with a high concentration of dissolved salt solids can “salt out” in the presence of alcohols. To help prevent the occurrence of this salt precipitation, do not exceed 20% by volume of isopropanol or 50% by volume of methanol in treating solutions.
- Incompatibility: Some crude oils are incompatible with both methanol and isopropanol. Conduct compatibility tests before acidizing a well with a fluid containing alcohol. Some formation types may be extremely sensitive to aqueous solutions that contain high concentrations of alcohols.
In some cases, formations should not be acidized with alcohol-acid solutions. The formation of undesirable methyl chloride is possible with HCl solutions that contain 30% or more methanol at bottomhole temperatures above 200° F.
Mutual Solvents
A mutual solvent is a material that is soluble in both hydrocarbon and aqueous solutions. It can help to solubilize an aqueous solution into a hydrocarbon solution or vice versa. Common mutual solvents include ethylene glycol monobutyl ether (EGMBE), diethylene glycol monobutyl ether (DEGMBE), modified glycol ethers (MGE), and also alcohol.
The use of mutual solvents, particularly EGMBE and MGE, in acid stimulation of a sandstone reservoir is a common practice. Mutual solvents have been used in postflushes because they help to:
- reduce water saturation from around the wellbore by lowering the surface tension of the water, thus preventing water blocks
- solubilize a portion of the water into the hydrocarbon phase, thus reducing the amount of irreducible water saturation
- provide a water-wet formation, thus maintaining the best relative permeability for oil production
- prevent insoluble fines from becoming oil-wet
- stabilize emulsions
- maintain the needed concentration of surfactants and inhibitors in solution by helping to prevent adsorption of these materials onto the formation
Mutual solvents have also been found to reduce the formation damage that can result from using corrosion inhibitors in acid treatments. The normal treating concentration of mutual solvents varies from 2 to 50% by volume, depending on the application. Most sandstone acidizing applications use 10% or less.