Learning Objectives
After completing this topic “Additives in Acidizing Fluids“, you will be able answer to:
- What is the purpose of using additives in acidizing process for oil well?
- Which acid is used in acidizing process?
- What are acid additives?
- What is iron control agent?
- How is HCl used in fracking?
- What is SandStone acidizing?
- What is in hydrochloric acid?
- What is stimulation in oil and gas?
- What is acid job in oil industry?
- How do you make hydrofluoric acid?
- What are the objectives of matrix stimulation?
By completing this topic and then applying the learnings in your job, you will be able to attain Basic Application Competence Level in Acidizing and Other Chemical Treatments.
Corrosion Inhibitors
The principal additives to acidizing fluids are corrosion inhibitors. A corrosion inhibitor is a chemical that slows acid corrosion on drill pipe, tubing, or any other metal that the acid contacts during treatment. Brief explanations follow of the acid corrosion mechanism, types of acid corrosion, and corrosion by different acid types.
Acid Corrosion on Steel: All uninhibited acid solutions corrode steel. The attack of acid on steel occurs through the dissociated hydrogen ion of the acid solution. This results in the oxidation and dissolution of iron at the anodic sites on the metal surface along with the reduction of hydrogen ions and formation of hydrogen at the cathodic sites:
Anodic Reaction (Oxidation)
Cathodic Reaction (Reduction)
These two reactions can be summarized by the following overall reaction:
This electrochemical corrosion process is shown in Figure 1 (electrochemical corrosion).
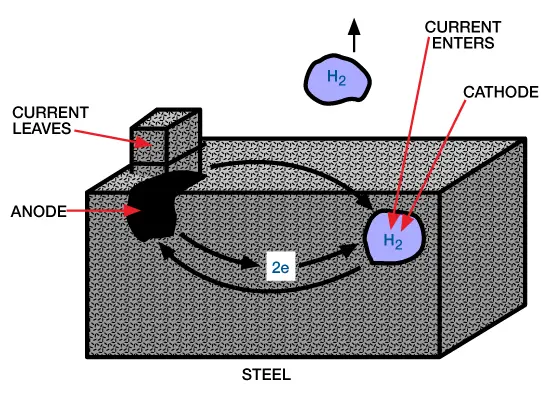
The units of measurement used to determine the amount of corrosion are To illustrate, one sq. ft of steel 0.001 in. thick weighs 0.041 lb.; 1.92 ft of 2-
in. tubing has an inside surface area of one sq. ft. If corrosion weight loss of this 2-
in. tubing is 0.041
, then every foot of the string has lost 0.021 lb. and is thinner by 0.001 in.
Acceptable corrosion limits are demonstrated in Table 1 (below). The range is from 0.02 to 0.09 of metal surface, depending on temperature. Keep in mind, however, that acids corrode more evenly, with less pitting, at higher temperatures. At elevated temperatures, then, more corrosion may be permitted with less chance of forming a hole in the drill pipe or tubing string. A corrosion limit of 0.10
may be acceptable with a low pitting index representing 1% metal loss. Furthermore, there is less risk in an initial completion acidizing treatment than on tubing subjected to repeated acidizing.
Temp.![]() | Corrosion Limit![]() |
---|---|
200 | 0.02 |
200-275 | 0.05 |
275-350 | 0.09 |
Since acid corrosion is strongly influenced by the chemical composition of the steel, metal chemistry is an important factor in corrosion studies on oilfield tubular goods. API specifications, however, are based on physical properties of the metal (i.e., tensile strength) rather than chemical composition. Marked differences in chemical composition may exist in the same grade of tubing or casing from different manufacturers, or from lot to lot from the same manufacturer.
A general rule to follow when comparing the degree of corrosivity of two types of tubular goods is that the higher the hardness of the metal, the more prone it is to acid attack. This rule is illustrated in Figure 2 (Effect of HCl on different types of steel).

Remember, however, that there are exceptions to every rule.
Types of Acid Corrosion: In uninhibited acid solutions, the corrosion of steel is usually uniform. The constant shifting of anodic and cathodic areas spreads corrosion more or less evenly over the entire surface of the metal. Pitting of the steel surfaces occurs in some situations due to inhibitor breakdown, insufficient inhibitor, and metal impurities.
Inhibitor Breakdown: On steel exposed to acid solutions containing an inferior corrosion inhibitor, a pitting type of corrosion is not uncommon. All corrosion inhibitors eventually break down after some period of time, depending on, among other factors, temperature, acid strength, and metal type. When this point is reached, an inferior inhibitor may actually tend to promote pitting by desorbing from the metal surface in localized areas.
Insufficient Inhibitor Regardless of the quality of corrosion inhibitor, pitting may also occur if there is an insufficient amount of inhibitor to effectively coat steel surfaces under certain conditions. Unprotected steel surface areas are rapidly attacked by the acid solution, and pitting occurs.
Metal Impurities: Another condition that promotes pitting is the presence of impurities or inclusions within the steel itself. For example, small pieces of slag may become trapped during the forming of the steel, or improper heat treating or quenching of the steel may produce discontinuities in its grain structure. These imperfections may, in turn, become anodic to the rest of the surrounding steel structure, and thus promote acid attack.
Hydrogen Embrittlement: This is one of the most insidious forms of corrosive attack. Because oxidation and dissolution of iron occur at the anodic sites on the metal surface when steel is corroded by acid, the reduction of hydrogen ions and formation of hydrogen takes place at the cathodic sites. The cathodic reaction can be expressed as
Because atomic hydrogen is very small, it can penetrate the metal and become lodged in void spaces along metal grain boundaries. Molecular hydrogen is too large to penetrate and lodge in these spaces, and is not a problem at well temperatures.
When atomic hydrogen that has penetrated the metal structure comes in contact with another atomic hydrogen atom, the two combine to form molecular hydrogen within the steel structure. When the larger molecule very slowly migrates out, extremely high pressures develop in the void spaces that literally split the metal open. This process is called hydrogen embrittlement.
If hydrogen sulfide (H2S) is involved, the splitting phenomenon is known as hydrogen sulfide cracking. H2S tends to slow down the transformation of atomic hydrogen into molecular hydrogen on the metal surface at the cathode. It thus allows greater penetration into the metal which, in turn, increases the probability of high-strength steel cracking. Figure 3, is a photomicrograph of a crack in stressed Pl05 pipe exposed to 15% HCl saturated with H2S.

This cracking can occur when very little physical corrosion is taking place. Most commercially available corrosion inhibitors are ineffective in controlling cracking of high-strength steels in acid saturated with H2S. As a general rule, steels with a Rockwell “C” hardness of 22 or less are not as likely to experience H2S cracking as steels with greater hardness.
Corrosion by Different Acid Types The most common types of acid solutions used in the oil field are HCl, formic, and acetic.
The degree of ionization of hydrogen from the acid molecule determines the acid strength, which is directly proportional to its corrosivity on steel. The degree of ionization for these acids is HCl > formic > acetic. HCl, then, is more corrosive on steel than formic, which is more corrosive than acetic. Quite logically, the more aggressive an acid is in its attack on steel, the more difficult it is to inhibit. The mechanism of attack, however, is the same for all three types, as shown below.
Inhibitor Types
There are two basic types of corrosion inhibitors: inorganic and organic.
Inorganic Corrosion Inhibitors: This class of inhibitor includes salts of zinc, nickel, copper, arsenic, antimony, and various other metals. Of these, the most widely used are arsenic compounds.
When these arsenic compounds are added to an acid solution, they “plate out,” or form iron sulfide at cathodic sites of exposed steel surfaces. These plates decrease the rate of hydrogen ion exchange, because iron sulfide acts as a barrier between metal and acid. It is a continuing process in which acid reacts with iron sulfide, rather than metal.
Some advantages of inorganic inhibitors are that they:
- work very effectively at high temperatures for long contact times;
- cost less than organic inhibitors.
Disadvantages of inorganic inhibitors are that they:
- tend to lose their effectiveness in 17 to 20% HCl and stronger acid solutions;
- react with H2S(via FeS ions) to form an insoluble precipitate called arsenic sulfide.(In the reservoir this precipitate exists in a gaseous state, but when it enters the wellbore and cools, a plugging solid forms.);
- poison refinery catalysts, such as platinum;
- liberate occasionally toxic arsine gas as a by-product of corrosion;
- resist mixing and safe handling.
Organic Corrosion Inhibitors: These inhibitors are composed of polar organic compounds capable of adsorbing onto the metal surface, thereby establishing a protective film that acts as a barrier between the metal and the acid solution. They usually serve as a cathodic polarizer by limiting the hydrogen ion mobility at cathodic sites. Organic inhibitors are composed of rather complex hydrocarbon units with one or more polar groups made of sulfur, oxygen, or nitrogen.
Some advantages of organic inhibitors are that they:
- can be used in the presence of H2S without precipitation of arsenic sulfide, which can plug the wellbore;
- do not poison refinery catalysts;
- work effectively in all acid concentrations.
Some disadvantages of organic inhibitors are that they:
- tend toward in-situ degradation – that is, they chemically degrade with time in the presence of an acid solution, and thus do not readily provide long-term protection at temperatures above 220° F.
- cost more than the inorganic corrosion inhibitors.
Table 2 (below) demonstrates effectiveness of organic and inorganic corrosion inhibitors at high temperatures in 15% HCl. The protective time reflects time required for the HCl to remove 0.05 of exposed metal area.
Table 2: Effectiveness of corrosion inhibitors at high temperatures in 15% HCl. | |||
---|---|---|---|
Type Inhibitor | Inhibitor Concentration-% | Temperature °F | Protection Time- hr.* |
*Time required for 15% HCl to remove 0.05 | |||
Organic | 0.6 | 200 | 24 |
1.0 | 250 | 10 | |
2.0 | 300 | 2 | |
Inorganic | 0.4 | 200 | 24 |
1.2 | 250 | 24 | |
2.0 | 300 | 12 |
Do not make the mistake of assuming that twice as much inhibitor provides twice as much protection: the concentration limit varies from one inhibitor to another. The general rule is that a 2% concentration is maximum. Beyond this point, no practical benefit is gained.
Remember that the purpose of a corrosion inhibitor is to slow the acid reaction rate on steel. Inhibitors in and of themselves do not prevent corrosion.
Listed in Table 3 are some examples of corrosion protection times available at the more common temperatures found in acidizing treatments.
Type of Inhibitor | Inhibitor Concentration | Acid Type | Acid Concentration | Temp. (°F) | Protection Time* |
---|---|---|---|---|---|
Low Temp. | 0.10% | HCI | 15% | 100 | 7 days |
Low Temp. | 0.15% | HCI | 15% | 150 | 2.5 days |
Low Temp. | 0.50% | HCI | 15% | 200 | 17 hrs |
Low Temp. | 1.00% | HCI | 28% | 200 | 21 hrs |
Medium Temp. | 0.50% | HCI | 15% | 200 | 28 hrs |
Medium Temp. | 0.80% | HCI | 28% | 200 | 44 hrs |
Organic Acid | 0.30% | Acetic | 10% | 200 | 90 days |

Table 3: Effectiveness of various organic corrosion inhibitors at common well temperatures.
Intensifiers
Although these additives cannot be considered inhibitors when used alone, their effectiveness is increased when they are used in conjunction with an organic inhibitor. The commonest intensifiers are potassium iodide, cuprous iodide, and formamide. The addition of these synergistic chemicals to existing organic inhibitor formulations greatly extends the range of their effectiveness, particularly in higher-temperature applications.